Industrial automation and the new-collar job
By Chris Johnson
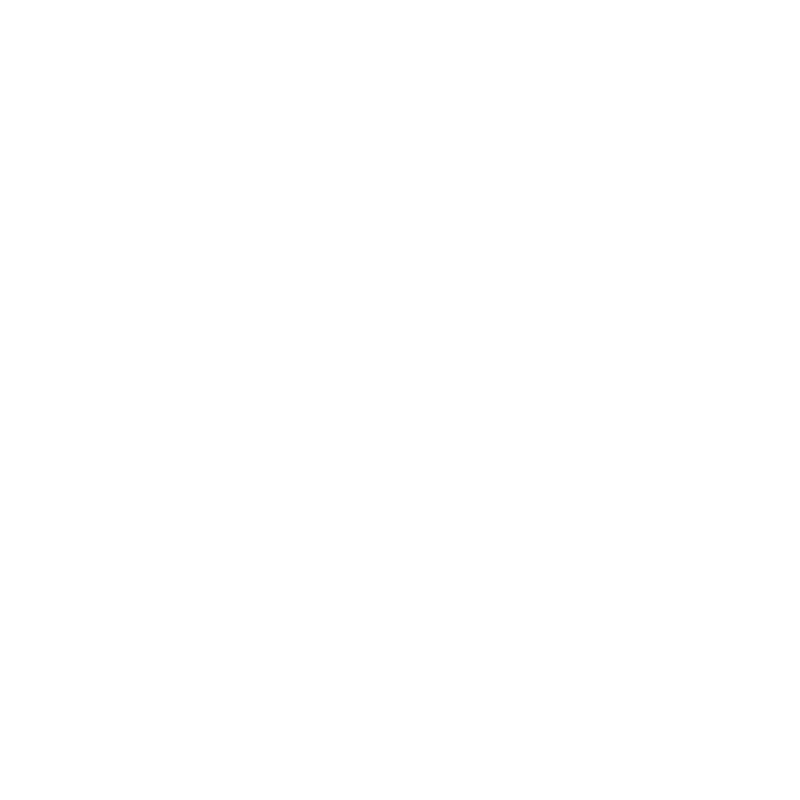
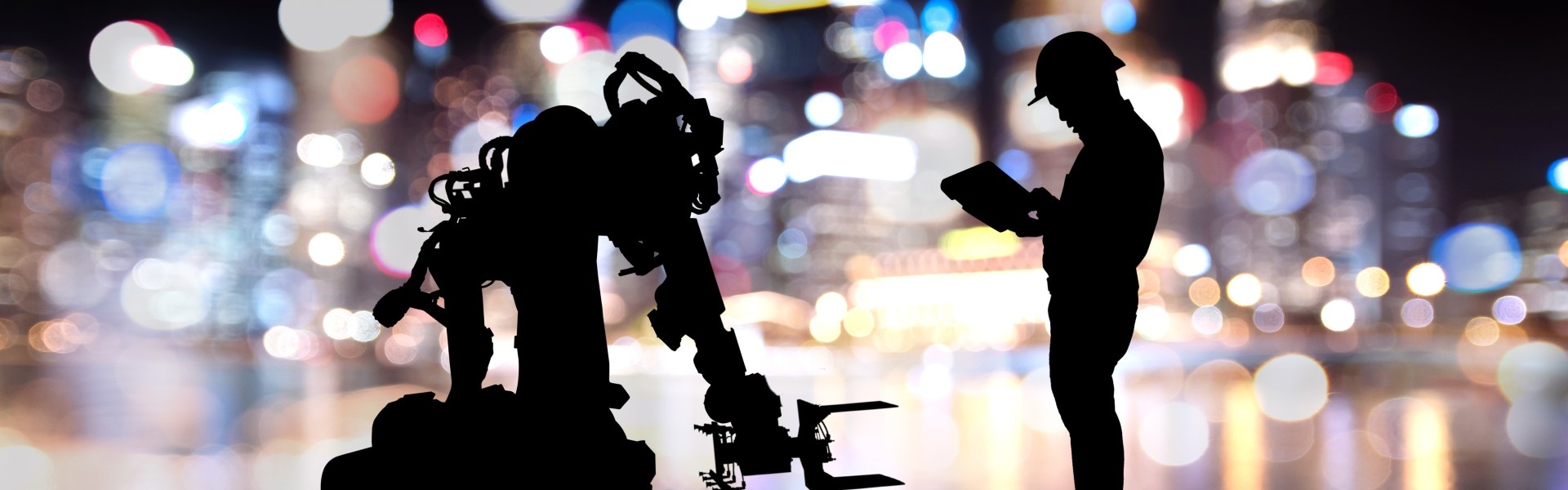
For the past 200 years, industrial revolutions have profoundly impacted how we work. Our modern, fourth industrial revolution promises the same.
Mechanization drove the first, kicking off in Great Britain in the mid-18th century. Workers left farms and poured into factories in big cities. Coal mining and the invention of the steam engine accelerated the buildout of railroads.
The second, late 19th century in America, gave us the internal combustion engine, powering our ships, cars and planes and making possible the mass mobility of people and goods.
With the invention of the industrial computer, in the mid-20th century, we entered the digital age and the automation of machinery and systems.
The fourth industrial revolution accelerated automation and added intelligence, with technologies like cloud computing, artificial intelligence (AI), machine learning (ML), augmented reality and more. And as digitalization and automation become the norm for asset-heavy industries, a world where people work hand-in-hand with machines is becoming the reality.
The impact of automation
While digitalization brings great benefits to the work environment, we can’t ignore the stigma that goes along with automation and “new” technical tools in the workplace. People worry that robots and automation technology will take away jobs. While it is true that some tasks previously done by humans will now be handed off to robots, the fact is that there simply aren’t enough humans available to do those jobs while at the same time ensuring productivity increases to handle market demand.
Attracting and retaining talent with newer, more productive and more satisfying ways of working for the digital generation will prove to be a key element for companies looking to assure the stability of their future workforce. According to a study by Dell, 80 percent of Gen-Z workers wish to work with cutting-edge technologies, and 91 percent take technology into account when deciding between employers.
Artificial intelligence, machine learning, robotics and the industrial metaverse are all expected to have a major impact on the future work environment, impacting everything from staffing and training to employee satisfaction. According to the World Economic Forum, more than a billion jobs are set to be radically transformed by technology by 2030.
We believe this industrial revolution will transform modern society and result in a new type of worker. Automation will augment the traditional cognitive, physical and clerical jobs – or colloquially, the white- and blue- collar jobs – and give us what’s being called the “new-collar” worker.
So how will industrial automation transform our workplace?
And what is the impact on workers?
The answers, in our view, center around two trends. One has to do with robotic automation and the second with augmentation of the worker.
Momentum in robotics
Robotic automation is about replacing predictable and dangerous tasks with smart, software-driven physical processes. We see this happening already in industries like mining, manufacturing, and logistics. Consider Peru’s Minera Las Bambas, which is expanding autonomous and remote operations in its open-pit copper mine to reduce the number of workers exposed to dangerous conditions and increase productivity. And Equinor, one of the world’s leading producers of oil, gas and wind power, is connecting offshore wind facilities, improving worker safety and maintenance operations.
These physical processes rely on sensors for improved flexibility, mobility and precision. And we leverage AI and ML to constantly improve the precision, speed and quality of the analytics software that drives this robotic automation. We are getting better and better at this, all the time.
Augmentation of the worker
In parallel, we are modifying the work environment, transitioning to one where humans are augmented by technology advancements. Advancements like:
- Remote control of equipment such as vehicles, gantry cranes or shunting engines.
- Sophisticated tools —like electronic wrenches that digitally control for torque, angle and log data – to control tasks.
- Augmented reality (AR) that uses multi-modal terminals.
- Wearables such as heads-up displays that provide precise task-based knowledge.
- Experts and mentors that assist remotely, with context-based knowledge resources available at the touch of a fingertip – eliminating in-class and in-field training.
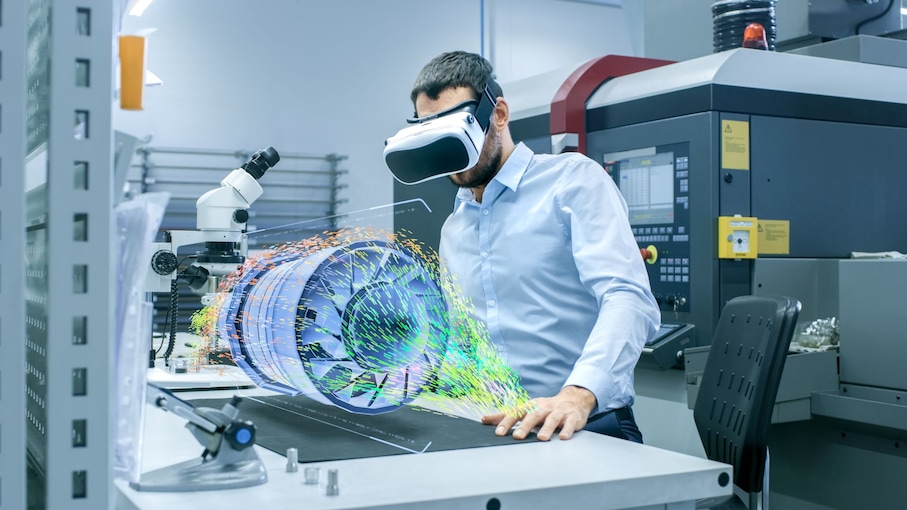
As automation and worker augmentation intersect, traditional physical “blue-collar” jobs will evolve. Jobs with a higher proportion of unpredictable tasks that require specialized expertise are more likely to be augmented, while repetitive tasks are likely to be automated.
The net effect is a shift in the workforce toward “new-collar” jobs handled by workers that blend human and machine skills and deliver a blend of cognitive and physical performance.
The evolution of work
After World War II, mass production and mass consumption became the norm. Suddenly, we could produce goods faster and cheaper, and they flooded the market, fueling one of the most significant shifts in living standards in our history.
Now, industrial enterprises must evolve again. Customer expectations are changing, supply chains are shifting, fundamental workforce demographics are evolving, and all industries must meet the world’s essential climate goals.
To meet these challenges, industry must add new elements of resilience, agility and adaptability to their operations – and new tools that make the elements actionable. The winners are already shifting processes and practices toward the nimble models of the software enterprise, implementing development and operational processes that equip them for rapid innovation and continuous development and optimization. New tools such as digital twins, industrial metaverse, AI, XR are being utilized to optimize operations – and this is just the beginning of what will define our new ways of working. The demand for the skills of digitalization will be high but so will the opportunity.
Critical connectivity is an essential foundation
While Industry 4.0 is built on some truly breakthrough technologies, at its heart is high-performance networking. Underpinning the critical communications that are essential for digitalization are agile, intelligent, high-speed connectivity networks built on high-performance wireless and IP/MPLS and optical transport infrastructure. Critical networks support the essential functions and services of a business, government, economy, or society – from first responders to power utilities, government networks to industrial networks, massive research networks to railway communications, and safety systems.
Organizations that want to modernize and transition to more digitalized and connected business models, and take advantage of the tools and applications of future industries, must shift their network infrastructures to flexible, high-performance networks providing ubiquitous, robust connectivity. Transport networks, edge cloud and interconnected data centers will be required to enable the processing of massive amounts of data necessary to support mission-critical operations and generate even deeper insights to further improve operations. End-to-end private wireless networks based on LTE, 5G and, in time, 6G will also be critical for supporting machine-to-machine communications, remote monitoring and management, and digital-physical fusion.
Digitalization is a fact of work and life. Thus, industries should prioritize lifelong learning and upskilling to attract and keep the best talent and remain competitive. Indeed, universities, educators, policymakers and technology companies must work together with industry partners to ensure that the workforce is ready to assume these new, more-fulfilling roles. 5G and the Industrial Metaverse can be harnessed for augmented and virtual reality technologies, which can support both the scope and scale of the training as well as the upgrades needed as we transform toward hybrid cognitive-physical work.
We are once again in the midst of an industrial revolution that will profoundly impact how we all work. Supported by an enhanced level of connectivity, the next decade will usher in unprecedented changes in worker augmentation, giving rise to the “new-collar” worker, leading to sizable boosts in overall productivity, efficiency, sustainability – and success.

About Chris Johnson
Chris Johnson is the Senior Vice President and Global Head of Enterprise at Nokia. A veteran sales and business leader, Chris focuses on delivering critical network solutions for the world's most essential industries.
About Nokia
At Nokia, we create technology that helps the world act together.
As a B2B technology innovation leader, we are pioneering networks that sense, think, and act by leveraging our work across mobile, fixed and cloud networks. In addition, we create value with intellectual property and long-term research, led by the award-winning Nokia Bell Labs.
Service providers, enterprises and partners worldwide trust Nokia to deliver secure, reliable and sustainable networks today – and work with us to create the digital services and applications of the future.
Media inquiries
Nokia Communications, Corporate
Email: Press.Services@nokia.com