The bumpy road to automation
Industries around the world are adopting a new wave of robotics called cognitive robots. These robots are more and more capable to fully move around factories, warehouses, and other dangerous and challenging environments in an autonomous manner. Their level of autonomy and cognition abilities vary from one solution to other. Most are using their onboard sensors and sophisticated technology to work with no human intervention.
While the technology is quite impressive, the automation world is still largely siloed. Each system makes its own decisions and does its own planning without knowledge of other systems’ decisions or plans. As a result, different operational technology (OT) systems are often at odds with one another. The more these robots are cognizant of their environments the more productive, resilient, and easy to operate they will become.
Enhancing robot connectivity and cognition
At Bell Labs, we believe the cloud-enabled metaverse will enable cognitive robots achieve their full potentials. The cloud will offer both the “information broker,” the analytics, and digital twin that drives actions and reactions in this fusion of the real-world and its virtual digital twin. Being connected to a ubiquitous and reliable network will allow for the flow of information from all sorts of onboard and IOT sensors to the cloud.
Our research focuses in two key areas:
Creating end-to-end solutions to sense, orchestrate and control multi-vendor mobile cognitive robots
Understanding the operational and safety requirements on connectivity and solving it not only in the network but at the far edge
Our Autonomous Mobile Robot solution
The Autonomous Robot Orchestration Solution provides a vendor independent unified fleet management system that hides the complexities of single robot management systems. It brings together multiple sub-systems to deliver the value of cloud-enabled cognitive robots. First, there is the sensing and localization system which aggregates data from multiple sources such as infrastructure cameras, radio-based localization systems and onboard robot sensors. The data is then pushed to the cloud to update the digital twin of the whole system of robots and the environment they operate in. Second, there is the analytics and path planning algorithms which feed an orchestration system of all the assets. The latter is our multi-vendor fleet manager. Finally, there are the actions taken by the system to meet the operational requirements of the factory through control of its heterogeneous fleet of robots.
Our system is completely cloud based and is built on effective sharing of knowledge and a collective reasoning and scheduling engine. We use the network as a sensor and infrastructure assets to augment the embedded sensors in each individual robot. The solution achieves optimal system-level performance through joint multi-robot path planning and adapts dynamically to any real-world situations encountered by the heterogeneous fleet of robots.
Real-world testing and validation
Nokia Bell Labs tested its orchestration solution at the Nokia factory in Chennai, India. We found that for every robot mission, the average distance traveled decreased by 28% after the trial began. In addition, the average time it took for a robot to complete a given task dropped by 40% for the first set of tasks. We have been continuously running the solution for over two years and are finding that the gains continue to hold and the factory can operate substantially more missions with the same robot fleet. With the orchestration system planning traffic flows in a holistic manner, the robots are stuck in fewer traffic jams and traversing routes that avoid both factory workers and other robots and vehicles. This has shaved both meters and minutes off their journeys while making factory operations safer.
Developing a resilient communication solution – the Cognitive Communication Hub
Any robotic orchestration system suitable for industry needs to manage hundreds if not thousands of individual, fully autonomous and automated-guided robots at any given factory or campus. Robots in industrial and enterprise spaces often encounter a heterogeneous mix of wireless networks as they traverse their environment, but off-the-shelf robot platforms are only capable of using a single radio access technology at a time. Our solution adds the ability for the far edge to connect to any network while maintaining the connectivity needs of the system to maintain safe and resilient operations.
The Cognitive Communication Hub, shown above, is added to some of the robotic assets that we managed in the Chennai factory. The hub guarantees resilient wireless communications between the robots and the cloud. The hub also senses the network in its variations and moves application data flows from one network to the other transparently to the robotic system. Although the hub’s primary goal is to provide resilient communications, the constant monitoring of the wireless networking landscape also facilitates the maintenance of the real-time network digital twin.
The hub is also used to carry out compute tasks related to cloud orchestration. The video feed of camera-based vision can both be used to synchronize the real world and digital twin, but also used for enhanced safety sensing and on edge ML analytics. This continuum between the edge and the cloud is our key to our vision.
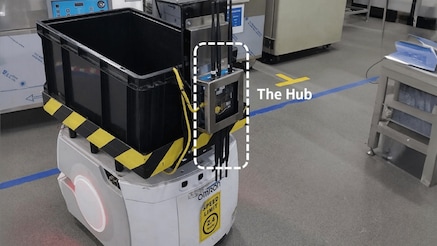
Learn more about our Entrepreneurs in Residence
programs and projects.