Lost tools, lost time: The true cost of missing equipment in manufacturing
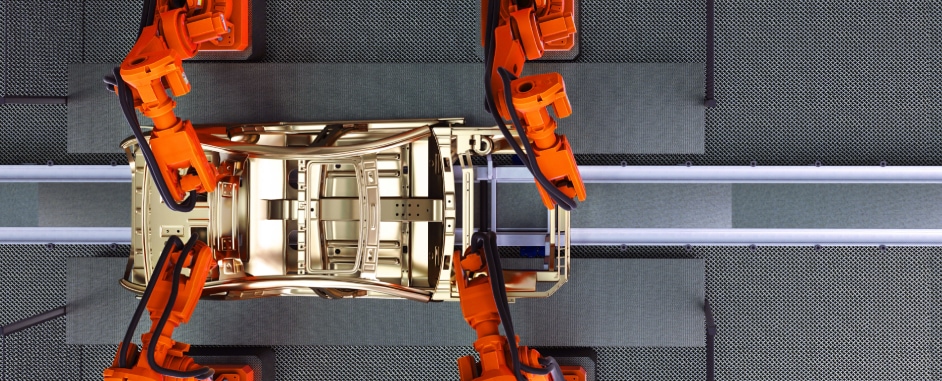
With hundreds of workers, sub-contractors, rigid production schedules, specialized equipment, vast storage areas and AGVs, AMRs and forklifts idling or traversing the floor, any manufacturing plant is a whirlwind of constant activity and requires precise coordination. However, even for ISO 9001-compliant companies and those adhering to other manufacturing quality standards, it’s easy to understand how tools and parts can be misplaced. But at what cost to the business? If every worker spends just 10 minutes each day searching for tools, that equates to 40 hours of downtime per worker annually. Leading tool supplier, Sandvik Coromant, calculates that 20 percent of worker productivity is lost searching for missing tools.
Manufacturers deal with countless tools across assembly, maintenance, inspection and quality control, and workers must access the right tool for a task at the right time to maintain production schedules, product reliability and compliance with quality and industry standards. In a facility where a diverse product range is manufactured, this issue is magnified and when tools or raw materials go missing, whether through error or theft, replacement costs will climb while productivity goes down.
Good inventory management also incorporates balanced tool usage. Sandvik Coromant found that 60 percent of tool stock is never used, meaning 40 percent is overused further bloating replacement costs. Lack of data about usage can lead to capital being tied up and downtime when vital tools are unavailable to complete a customer order.
While poor tool management isn’t the sole cause of downtime, in a high-value production environment – think automotive or aerospace – it can be costly! An hour’s downtime at an automotive plant can cost over $2 million (Siemens). A worker stepping out of a vehicle production line to search for the right tool for 20 minutes comes at a high price. But so does using the wrong tool. It can lower product quality, risk compliance breaches and for certain sectors like the pharmaceutical or food processing industry, it can lead to product cross-contamination. All of which can potentially result in defective products that risk customer safety.
Global manufacturers with multiple sites can see the cost of poor tool management rise exponentially. So how can you address this issue? The answer is to enable real-time asset tracking.
The benefits of real-time asset tracking
Using an industrial asset tracking solution, you can pinpoint all critical tools and production equipment, ensuring they are where they need to be. This allows you to recover valuable lost time and ensure workforce availability to maintain productivity and efficiency:
-
Enhance traceability and maintain quality control and regulatory compliance, ensuring only the correct tools are used and no steps in the production process are skipped.
-
Track and balance tool usage to reduce bloated maintenance and replacement costs.
-
Monitor and manage stock levels based on your actual requirements, ensuring capital isn’t tied up unnecessarily and you have adequate stock of the tools you use most.
-
Benefit from alerts triggered when a tool is removed from a defined space or stored incorrectly to reduce the costs associated with tool theft and replacement.
Choosing the right solutions
There are many ways for manufacturers and other industry sectors to take advantage of asset tracking. Which solution you choose will depend on your unique business requirements, your industry, and the space and layout at your site. Real-time tracking and positioning deliver enhanced visibility to your operations to help you oversee and monitor worker tools and usage, raw materials and finished goods, lone workers, and mobile assets such as trucks or AMRs (Autonomous Mobile Robots) to improve productivity, efficiency and profitability.
At Nokia, we’ve created a comprehensive portfolio of technologies and applications designed to satisfy the diverse tracking and positioning needs of many industries, site layouts and business challenges:
-
Nokia Visual Position and Object Detection is a tag-less tracking solution that leverages your existing cameras and uses AI-powered positioning of people and objects based on real-time video feeds
-
Nokia High Accuracy Indoor Positioning (HAIP) uses high-precision Bluetooth technology to pinpoint people and objects indoors.
-
HERE HD GNSS uses Global Navigation Satellite Systems (GNSS) to deliver high-accuracy outdoor tracking.
-
Nordic ID is a complete Radio Frequency Identification (RFID) solution that delivers high-velocity asset tracking indoors and outdoors.
-
Portalify Smartview leverages workers’ smartphones to enable lone worker tracking indoors and outdoors.
All applications run on our on-premises MX Industrial Edge (MXIE), so you benefit from real-time on-site data processing and full visibility into your operations. MXIE is powered by Intel® Xeon® processors, which deliver the high performance required to process and analyze your growing volumes of business-critical data. Integration of your chosen solution is further simplified as our partner, Wipro, provides strategic guidance, end-to-end design, implementation and managed services.
Download our free guide to discover the benefits of real-time tracking and positioning and see how, together with our partners Intel and Wipro, we can help you achieve your manufacturing digitalization goals.