“Plug and produce” – the new normal for 5G-powered smart factories
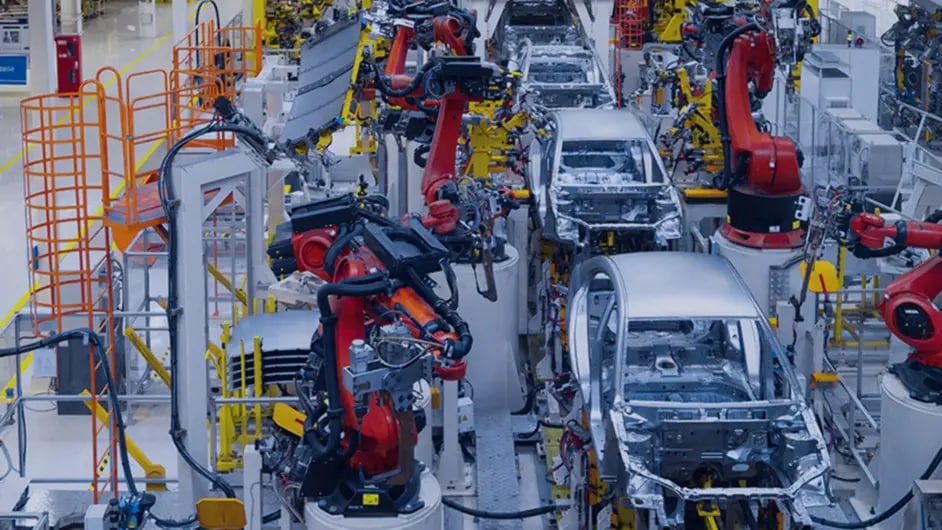
Industry 4.0 introduces the smart factory as a key solution to improve flexibility in manufacturing processes to address dynamically changing market needs and improve the robustness and efficiency of production. The smart factory will usher in a new wave of “intelligent manufacturing,” using mass-scale connectivity, ubiquitous sensing and a heavy reliance on data to create more adaptable, resource-efficient and ergonomic manufacturing facilities. A critical enabler for the smart factory is scalable and pervasive connectivity between machines, people and objects, for which wireless connectivity will play a pivotal role. 5G networks are positioned by industry organizations, such as the 5G Alliance for Connected Industries and Automation (5G-ACIA), as the enabler for this vision and the use of 5G is forecasted to create more than $1 trillion in new value by 2028 by enabling the modernization of industries and the Industrial Internet of Things (IIoT).
Enabling seamless integration of 5G in existing factories boils down to simply plugging your Ethernet cable into a wireless terminal instead of an Ethernet bridge.
Two major roadblocks to using wireless connectivity have been removed with the move to 5G technology. First, 5G introduced support for Ultra-Reliable Low-Latency Communications (URLLC), which extends wireline robustness and speed to the wireless link, providing down to sub-millisecond latency achieved with 99.999% reliability (five nines) in Release 15 and 99.9999% (six nines) in Release 16. Second, in Release 16, Nokia led the industrial 5G related work on Time Sensitive Communications (TSC). TSC extends URLLC to full determinism support, controlling the exact delivery time of a packet with sub-microsecond accuracy and enabling all end devices in the network to be tightly time-synchronized. TSC provides packet transport with QoS characteristics such as bound on latency, loss and reliability. It should be noted that for many applications, sub-millisecond latency is not required making deterministic communications also applicable in larger networks.
To be successful in driving the Industry 4.0 vision, however, the 5G system must work in harmony with the technologies used for communication in vertical industries such as industrial automation networks. The IEEE Time Sensitive Networking (TSN) set of specifications is considered the convergence technology that will enable deterministic and low-latency communication in the factories of the future. 5G Release 16 fully supports integration into an existing industrial Ethernet network running IEEE TSN and automatically adapts its network scheduling to the service schedules of the TSN system. Hence, 5G blends in well with existing network infrastructure – making the use of 5G mobile networks in a production line as easy as plugging in an Ethernet cable.
The 5G solution is built on a Nokia Bell Labs innovation where 5G mimics an IEEE TSN bridge, supporting transparent integration into the vertical management system and with an extended quality of service framework that ensures full determinism over wireless connections. The solution has been conceived in close collaboration with industrial partners as part of funded research projects, including the Tacnet 4.0 project funded by the German Federal Ministry of Education and Research (BMBF).
In order to understand how 3GPP 5G Rel 16 solutions can be adopted to seamlessly integrate 5G for industrial automation, read our whitepaper “5G plug-and-produce”. This whitepaper explains the ease of enabling 5G technology in the production line. Hence, cable connections are replaced with 5G connectivity and new use cases are enabled without re-designing or re-deploying industrial networks. The paper demonstrates what can be achieved if the telecommunications industry sets its mind to the critical technical challenges faced by industry verticals. A comprehensive overview of the tools and features standardized in Release 16 show how 5G can be integrated seamlessly into “brownfield” IEEE TSN deployments and offer novel disruptive services to automate industrial production. Furthermore, the paper provides an overview of technologies enabling wireline latencies far below 1ms with 5-6 nines of reliability and synchronization precision and jitter control below 1µs. For a comprehensive overview of 5G features introduced in Release 16 and 17, (some of which are essential also for IIoT use-cases), please see our other recent white paper “5G Release 16 and 17 in 3GPP”.
Ensuring more efficient and flexible production is a constant goal for industries, and in these unprecedented times of pandemic those goals become even more pressing. Smart factories will help bolster the supply chain and allow industries to shift production to critical goods, while helping minimize direct human interaction. 5G and TSC will be critical enablers to build smart factories of the future.