Six key digitalization trends that are transforming mining transportation
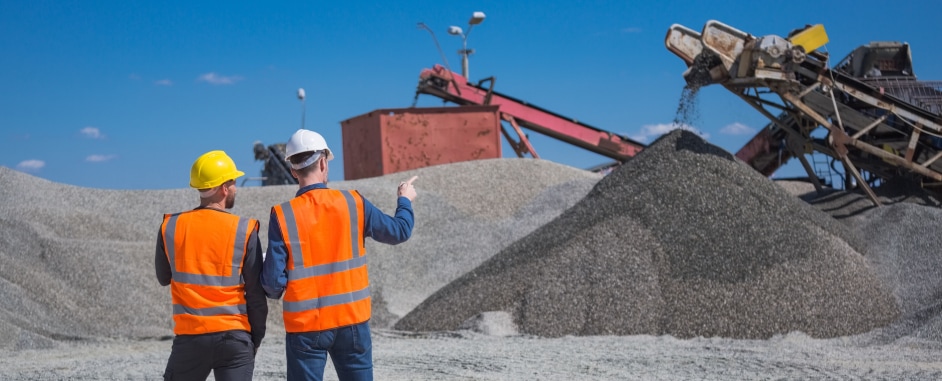
Mining is vital for the global economy, and today, digitalization is having a transformative impact on the industry worldwide. Did you know that by the end of 2025, over 13 billion dollars will be spent on mining digital transformation? This doesn’t just focus on operations at the mine but also encompasses the transportation infrastructure used to connect mineral-rich regions like Latin America to world markets.
By investing in the digitalization of their transportation networks, mining companies can, depending on various factors, improve productivity by about 20% through reduced logistic costs and increased efficiency.
This article examines the top digital trends in mining transportation, the impact of new technologies on the industry, and the opportunities that mining companies can capitalize on for a safer and greener mining future.
The importance of digitalization for mining transportation
Fluctuating commodity prices, strict environmental regulations, market access, and rising operating costs can impact the profitability of mines, and by optimizing transportation logistics from the pit to processing plants, companies can reduce that impact. Digitalization makes this possible and results in:
-
Improved operational efficiency through streamlined processes that minimize delays.
-
Increased worker safety through better monitoring and control.
-
Enhanced operational sustainability through optimized transportation routes that also reduce environmental impact.
-
A greater competitive advantage as companies become more agile and responsive to market changes.
So, how can this be achieved? As we look at key digitalization trends in mining transportation, I will explore the digital technologies being introduced, how they are being used, and their impact on the future of mining.
A deep dive into key digitalization trends in mining transportation
1. Autonomous Haulage Systems (AHS)
Autonomous Haulage Systems (AHS) represent a paradigm shift in mining transportation, transitioning the industry from its reliance on manned vehicles to self-driving giants. These systems utilize advanced technologies, including GPS, LiDAR, radar, and control algorithms, and allow vehicles to be controlled without human assistance. By adopting AHS, mining companies benefit from:
a. Safety Improvements: By removing the number of people working alongside the huge heavy haulage vehicles at mines and across difficult and dangerous terrains, companies can reduce the potential for worker accidents. Additionally, as worker fatigue and human error are no longer a factor, mining transportation becomes safer, and business interruptions and the associated costs are minimized.
b. Increased productivity: By operating AHS 24-7, companies can maximize performance and minimize downtime. This uninterrupted operation optimizes material handling and overall mine productivity, resulting in increased profitability.
c. Cost reduction: Companies implementing AHS decrease fuel consumption by around 9%, through strategic acceleration, braking, and coasting.
d. Improved efficiency: AHS can calculate the most efficient route paths, considering factors such as terrain and traffic to optimize routes. Autonomous vehicles can be rerouted more rapidly, leveraging data from many sources to minimize driving time and fuel consumption.
2. Predictive maintenance enabled by data-driven intelligence and advanced analytics
Data is essential for digitalization, and mining operations and transportation generate huge amounts. By implementing modern analytics platforms that can access and use this data, mining companies can gain valuable insights for decision-making. Predictive maintenance is perhaps one of the most critical applications enabled by these platforms. This uses sensor data from vehicles and systems to predict failures before they occur. This proactive approach results in:
a. Minimized downtime: By proactively scheduling maintenance before failures occur, unplanned downtime is significantly reduced, ensuring continuous operations for maximum productivity.
b. Optimized maintenance schedules: With access to data-driven insights, companies can schedule maintenance work when equipment and vehicles aren’t in demand, minimizing operational disruption, increasing efficiency, and reducing costs.
c. Extended equipment life: By solving problems before major failures occur, companies can extend the life of expensive equipment and vehicles. One Nokia partner company in Latin America has saved $80 million in annual costs.
3. IoT-enabled connected fleets deliver real-time visibility and control
The Internet of Things (IoT) has revolutionized the way mining companies manage their transportation fleets. Sensors in vehicles and equipment transmit real-time data about locations, speed, fuel consumption, tire pressure, engine performance, and more. With a connected transportation fleet, mining companies can:
a. Gain Real-time visibility: Operators get a complete real-time overview of their equipment and vehicles to efficiently, track, manage and respond to changing conditions, and make proactive adjustments to optimize journey times and resources.
b. Optimize resource allocation: Real-time data enables dynamic resource allocation, allowing companies to balance vehicle and equipment usage and avoid the bloated maintenance costs when some equipment and vehicles are used more than others. Dispatchers can make informed decisions about vehicle assignments and routes based on multiple factors and requirements.
c. Improve safety: Real-time alerts about the weather, unsafe driving conditions, deviations in driver behavior, or equipment malfunctions enhance safety protocols. This proactive approach allows for immediate intervention, mitigating risks and preventing accidents.
4. Integrated drones for aerial surveillance
Drones have become an integral part of digital mines as they can be dispatched to collect valuable data efficiently and cost-effectively. Drones equipped with high-resolution cameras, LiDAR sensors, and other tools can carry out detailed and regular surveillance of mining sites, transportation routes, and nearby areas for:
a. Route optimization: Drones can determine optimal transportation routes based on terrain, obstacles, and other factors to minimize travel time and fuel consumption. This data can also be used to plan new routes.
b. Infrastructure monitoring: Regular inspections of transportation routes, bridges, and other infrastructure can allow operators to identify damage or potential hazards before they impact safety or productivity.
c. Volumetric analysis: Drones can accurately measure inventory levels and material movements, providing valuable data for production planning, tracking project progress, and identifying operational bottlenecks.
5. Digital twins and real-world Simulations
Digital twins - virtual representations of physical assets and processes - are changing how mining companies plan and manage their transportation networks. By creating a digital replica of the entire transportation system, companies can:
a. Simulate scenarios: Companies can test various operating strategies, equipment configurations, and route options in a virtual environment and identify and remove potential bottlenecks, before implementing them in the real world.
b. Optimize Route Planning: By simulating multiple routes in the digital twin, companies can select the most efficient one based on travel time, fuel consumption, and terrain for cost savings and productivity gains.
c. Enhance Training Activities: Digital twins provide a safe environment for training drivers in real-world emergencies and on expensive equipment without real-world risks. This improves operators' skills and reduces the likelihood of errors.
6. Intelligent automation unlocked through artificial intelligence (AI) and machine learning (ML)
AI and ML can further enhance the possibilities of digitalized mining by identifying patterns from large amounts of data to predict future trends and automate complex tasks. Applications include:
a. Predictive maintenance: AI and ML can improve the accuracy of predictive maintenance models by recognizing subtle patterns in sensor data that traditional methods may miss for even greater machine uptime and much-reduced disruption.
b. Autonomous navigation: AI and ML improve autonomous transportation systems by enabling more sophisticated decision-making in complex environments where data must be analyzed in large amounts very quickly. This enables autonomous vehicles to operate more safely and efficiently.
c. Route optimization: AI and ML can be used to develop dynamic route optimization algorithms that adapt to changing weather and traffic conditions, or equipment availability, in real time.
Future trends and challenges for mining digitalization
The digitalization of mining and mining transportation is rapidly transforming the industry. New technologies like AI, blockchain, and augmented reality will change mining logistics forever. AI will become a major player in mining transportation, advancing capabilities in predictive maintenance and real-time route optimization to make mining transportation more efficient and reliable. Blockchain will change how resources across the supply chain are tracked, making the process safer and more transparent. Augmented reality (AR) will also play a significant role, giving operators greater visibility into their operations to make faster and better-informed decisions. AR dashboards and remote monitoring will improve logistics between the mine and the market.
As companies integrate these technologies as part of their digital transformation, they will benefit from more efficient and productive operations and reduced costs, and they can enhance the sustainability of their operations.
While digitalization offers numerous benefits, companies that want to adopt it for mining transportation will also face significant challenges:
-
High initial investment - Implementing digital technologies often requires significant upfront investment, which can be a barrier for some companies.
-
Data integration issues - Integrating data from different sources can be complex, especially for companies reliant on legacy systems and technologies.
-
Skills gap – The demand is growing for workers with new skills who can manage and analyze digital technologies.
-
Change management - Switching to digital processes requires a cultural change, which can be met with resistance from employees.
Reshaping mining transportation
Digitalization is reshaping mining transportation and giving companies the tools to improve efficiency, safety, and sustainability. From automation and IoT to data analytics and blockchain, new technologies are driving significant improvements in operational performance. As the mining industry evolves, companies that embrace digitalization will be better equipped to overcome challenges and seize opportunities in an increasingly competitive environment. That’s why the future of mining transportation lies in the successful integration of these digital technologies, and they will pave the way for a more efficient and sustainable industry.
Nokia Pit-to-Port Solution
Nokia’s digitalization solution for pit-to-port operations integrates advanced connectivity and automation technologies to streamline the movement of materials from mines to ports. Leveraging industrial-grade private wireless networks, the solution enables seamless communication between critical machinery, vehicles, and personnel and ensures efficient and safe operations even in the harshest environments. It incorporates IoT sensors, AI-driven analytics, and edge computing to provide real-time insights across operations for optimizing logistics, reducing fuel consumption, and minimizing companies’ environmental impact.
The unified platform supports a range of use cases, including autonomous vehicle operation, remote equipment monitoring, predictive maintenance, and enhanced worker safety through geo-fencing and smart wearables. By addressing the unique challenges of mining transportation with robust connectivity and data-driven tools, the Nokia solution empowers companies to achieve significant cost savings, improve operational reliability, and accelerate their Industry 4.0 transformation.
Contact us to discover how Nokia solutions can support pit-to-port digitalization for your mining operations.