Why OT edge is private wireless’s best friend
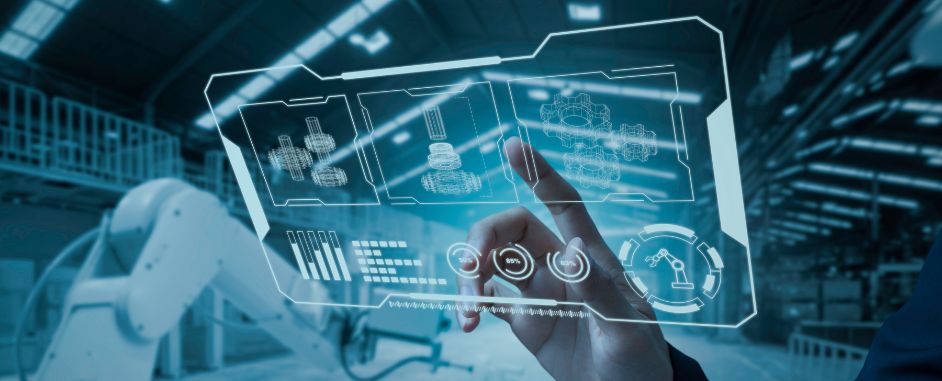
When we deployed the world’s first private wireless networks back in 2011, little did we know what kind of learning journey we were embarking on to try to understand all the specificities, needs, lingo and use cases of different industrial segments.
Coming from the telco world, where connectivity was the essence, we quickly learned how unconnected things and workers were in all these markets. However, we found that one of our technologies – 4.9G/LTE, in the form of private wireless networks – was the perfect fit to provide the pervasive, reliable and predictable wireless connectivity that industrials needed to easily connect all their assets and transport their critical operational technology (OT) data. Today, private wireless is recognized as a key element for any enterprise seeking to start an Industry 4.0 transformation.
Our next humbling learning moment was gaining an appreciation of the value and potential of the data we were transporting. While private wireless is critical for creating ubiquitous connectivity, the data it carries could make a true difference. With this data, an enterprise could gain direct insights into its plant operations or save millions of dollars by predicting a machine failure and avoiding a plant shutdown. More importantly, it could save a worker’s life and help reduce the industrial plant’s environmental impact.
The key to unlocking all this value is to combine a private wireless network that can carry the data with an OT edge that can compute the data to give it meaning and generate actionable insights.
Industry 4.0 requirements point directly to the edge
Industrial enterprises that want to embrace Industry 4.0 must pursue their digital transformation objectives while continuing to satisfy the “must-have” requirements of their OT systems. They can realize many of these needs and objectives by processing data on site and at the edge using an OT-grade edge solution.
Continuous operation is one of the key expectations of OT systems. It requires communications networks that can deliver the highest reliability and availability while keeping data local and secure. This is possible only with an on-site edge solution that can remove all dependencies on external factors (for example, external connectivity) and process data locally.
When it comes to realizing digital transformation objectives, only local processing of OT data can achieve the latency that machines and processes require. This also points to the use of an OT edge, coupled with the predictable performance and reliable connectivity that a private wireless network provides.
Figure 1: On-site OT edge supports most Industry 4.0 objectives and prerequisites
An interface to a complex, heterogenous and fragmented environment
The industrial plants where we deploy private wireless networks are brownfield campuses. They typically present a very complex environment on the southbound side, which can include machines, sensors, workers and vehicles.
Several factors contribute to this complexity. First, proprietary machine protocols and languages are commonplace. For example, more than 40 L2 machine communication protocols are being used, and while some of these protocols were meant to become standards, most remain as of today and few are very widely adopted. Second, each plant has many machines that come from different original equipment manufacturers (OEMs) and are made up of components (e.g., programmable logic controllers, sensors, actuators, drives) from many other automation and machine component OEMs. Third, many industrial machines or machine sub-modules integrate some sort of compute. Machines can last 30–70 years in a plant, so most plants still use many legacy machines with their own on-board compute units and legacy operating systems (OSs).
The picture is a bit simpler on the northbound side (plant level), but there are still many players providing software for plant management (e.g., manufacturing execution systems, operational overviews (e.g., digital twins, Industrial IoT dashboards), data analytics (e.g., predictive maintenance) and machine management (e.g., automated guided vehicle fleet management). Some of this software runs locally, in onsite or offsite enterprise data centers, or even in the cloud. Finally, machine OEMs, systems integrators, maintenance companies, suppliers and others require access to the data to get the information they need to supervise their part and keep everything running smoothly.
Private wireless provides the robust and reliable connectivity required for real-time OT data. But as explained earlier, there is a basic need for simplification to create the bridge between southbound and northbound. This means providing the right interfacing, translation, encapsulation so that the real-time data can be carried to the various elements in the right “protocol” and “language.” Simplification by creating an interface from all to all is a key role that an OT edge can play.
As we introduce an edge to an industrial environment, we can help take simplification further by migrating isolated, often legacy, processing units to it. Over time, the on-premises edge stack can become the main plant OT data processing unit.
Tackling Industry 4.0 transformation steps
Industry 4.0 transformation is long endeavor that, like previous industrial revolutions, is expected to take several decades to accomplish. There are four key steps to this transformation. An enterprise will need to repeat these steps many times to transform all of the OT processes in a single plant.
The first logical step is to “see” by creating a real-time digital image of the physical OT assets. Once real-time data is flowing, the second step is to “understand” by transforming information into knowledge that allows the enterprise to understand what happens in the plant and react quickly as things change. The third step is to “predict” by applying artificial intelligence and machine learning to the knowledge to understand what a pattern will mean in a few minutes, hours or days and predict things before they happen. Once an enterprise has built trust in these first three steps, the final step is to enable “autonomous actions,” where the digital technologies drive real-time activities.
Private wireless and industrial devices provide a foundation for these transformation steps by connecting all the machines, systems, sensors and workers in the plant. They form the nervous system of the plant by getting real-time data from these assets and, eventually, sending instructions to them.
The on-premises edge, and the applications running on it, act as the plant’s brain throughout the four transformation steps. Together, they take care of the transformation from information to knowledge, and from knowledge to wisdom and eventually drive the autonomous actions.
Figure 2: The four key steps to Industry 4.0 transformation
One platform for industrial digitalization
We believe that the combination of private wireless and edge is the key to kickstarting and enabling Industry 4.0 transformation. That’s why our private wireless solutions come with Nokia MX Industrial Edge (MXIE), the industry’s first off-the-shelf OT edge.
Many major analyst firms also believe there is a very close tie between edge and private wireless – and that enterprises will deepen their investment in the two technologies. For example, Analysys Mason forecasts that private wireless-attached edge will generate more than 6 billion euros in spending worldwide in 2030. In addition, analyst firms say that the majority of enterprise data will be processed on edge. By processing data close to the data source, enterprises can get the low latency they need for collaboration between cyber-physical systems, gain the ability to drive actionable intelligence for industrial automation and meet the reliability requirements of their OT.
Find out more
Visit our website to learn how you can unlock the potential of Industry 4.0 and transform your business to the power of n with a digitalization platform that brings private wireless and OT edge together to work as one.