Responsible Sourcing
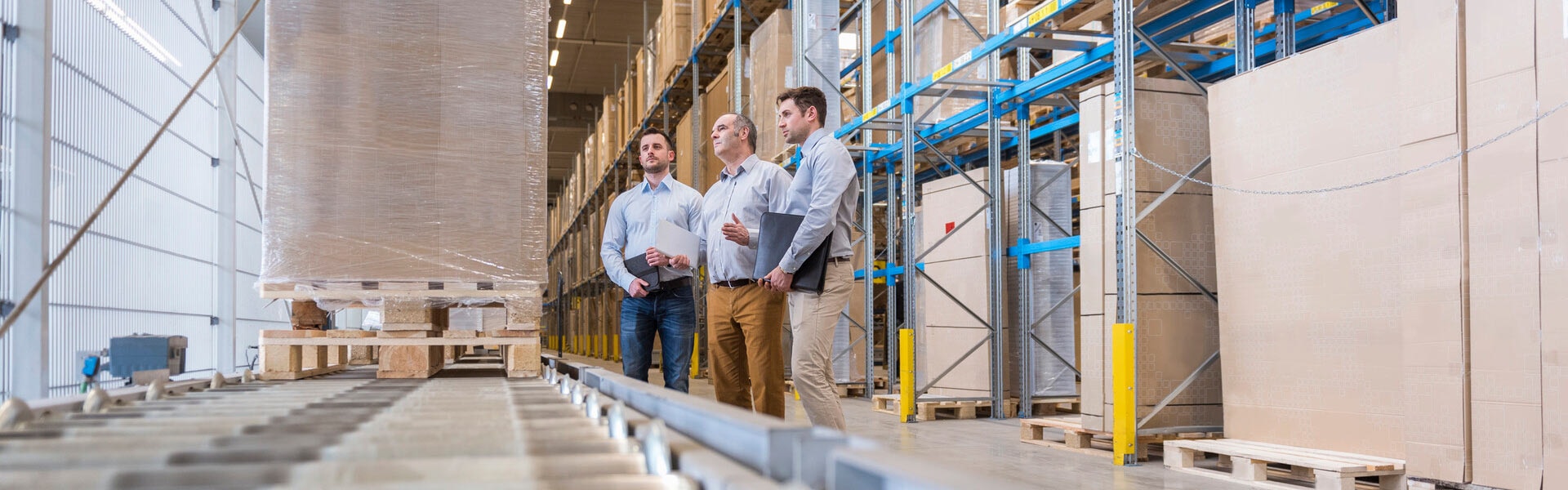
We drive active engagement across our value chain, working with our suppliers to raise the standards in our ecosystem in key ESG areas like the environment (climate and circularity), labor rights and ethical behavior. We have designed our sustainable sourcing program around four core pillars based on materiality assessment and group sustainability priorities: Supplier Due Diligence, Climate, Circularity, Responsible Minerals Sourcing, complemented by supplier development and learning and industry collaboration as key enablers for success.
We work with our suppliers to develop, innovate and build capability to enable a more sustainable and transparent ecosystem. We engage with our customers to drive improvements and share best practices in our common supply chain as well as collaborate across the ICT industry for greater impact.
Our supply chain approach
Robust procedures and processes
Robust procedures and processes
We have robust procedures and processes in place, and we continually improve them where necessary. These are supported by clear, well communicated policies. We identify and understand the risks associated with our supply chain and build and implement the programs and actions that help mitigate those risks. We employ a variety of audits and assessments to verify the integrity of our supply chain. We engage and increase supplier capabilities through learning and where necessary instigate remediation activities. We maintain a Corporate Responsibility risk map of our suppliers which we update regularly.
We have robust procedures and processes in place, and we continually improve them where necessary. These are supported by clear, well communicated policies. We identify and understand the risks associated with our supply chain and build and implement the programs and actions that help mitigate those risks. We employ a variety of audits and assessments to verify the integrity of our supply chain. We engage and increase supplier capabilities through learning and where necessary instigate remediation activities. We maintain a Corporate Responsibility risk map of our suppliers which we update regularly.
In 2024, we had business with around 9 300 suppliers, and 80% of our total supplier spend was distributed across around 400 suppliers. Our suppliers fall into six broad categories:
- final assembly suppliers
- hardware suppliers for product materials (such as standard components, optical components, semiconductors, electromechanical)
- market services suppliers who support the provision of services to our customers such as in installation and construction,
- managed services around the networks we sell
- IT suppliers
- indirect sourcing suppliers for everyday goods and services we need to run our business such as consulting, legal and marketing.
Our manufacturing suppliers are mainly based in Asia and services suppliers are based around the world. In 2024, in addition to its own factories in Finland and India, Nokia’s electronics manufacturing services final assembly suppliers included Flex, Foxconn, Jabil, Sanmina, Fabrinet and Karel supplier sites in Canada, China, Hungary, India, Italy, Malaysia, Mexico, Romania, Thailand, Turkey, the US and Vietnam.
A list of our largest strategic Original Design Manufacturers (ODMs), Original Equipment Manufacturers (OEMs) and Components suppliers are published on our website to further increase stakeholder transparency.
Sustainability is one of the six pillars of our Supplier Performance Evaluation (SPE). The supplier’s sustainability score in our SPE is composed of assessment results from the CDP Supply Chain Climate Change and Supply Chain Water Security assessments, EcoVadis sustainability assessments, the Nokia Responsible Minerals Sourcing program, the Nokia health and safety Supplier Maturity Assessment (SMA) and our own on-site corporate responsibility audit program.
We aim for 80% of our suppliers to have satisfactory SPE scores by 2025. In 2024, 78% of our suppliers had satisfactory scores across these sustainability programs, so we are on track, and we continue our work to grow the percentage.
We have detailed KPIs and public sourcing global targets, including supply chain climate targets as part of our 1.5°C climate commitment. All our supplier-related sustainability targets are listed in the “Our ESG targets and performance” section.
In addition to our own programs and assessments, we are part of industry coalitions, and work to improve the corporate responsibility of global supply chains. We have been a member of the Responsible Business Alliance (RBA) since 2021 and join its key workstreams. The RBA is the world’s largest industry coalition dedicated to CSR in global supply chains.
We are also one of the founding members of the First Movers Coalition – which is tasked with creating the market and spurring growth by leveraging collective demand and committing to buying zero-emission goods and services across eight critical industry sectors by 2030.
We expect our suppliers to adhere to our Third-Party Code of Conduct and we provide them with our supplier requirements, including the Responsible Business Alliance (RBA) Code of Conduct and additional, Nokia-specific sustainability requirements. The requirements cover topics such as environment, health, safety and security, privacy, risk management, labor and human rights management, ethics, and anti-corruption. They are communicated to our suppliers and integrated into our contractual requirements. An overview of these requirements can be found here.
We encourage our tier one suppliers (including our final assembly, materials and services suppliers) to apply and cascade the same requirements to their own suppliers. We check this through audits and EcoVadis documentation audits. Transparency and compliance requirements are firmly applied to all supplier relationships, and gifts or entertainment are neither given nor received beyond nominal value items. We investigate and qualify all suppliers, requiring them to comply with all applicable laws and regulations, and show they share the values stated in our Code of Conduct. Ethics and anti-corruption related requirements for our suppliers are detailed in our Third-Party Code of Conduct.
Incident reporting includes the compilation of occupational health and safety incidents occurred during 2024. These are investigated and tracked internally by Nokia People Safety and Security team. Nokia has revised its fatality reporting criteria in 2023 to include third parties such as members of the public who are assessed as being impacted by an incident that is deemed within Nokia’s control. This more closely aligns Nokia’s reporting with some of its closest industry stakeholders and competitors.
In 2024, there were 6 (six) work-related fatal incidents. These include 0 (zero) work-related fatal incidents involving Nokia own workforce, 5 (five) work-related fatal incidents involving contractors/subcontractors and 1 (one) work-related fatal incident involving a third-party. We want people to go home safe at the end of the day and we have a specific target of zero critical or fatal incidents among own workforce, suppliers and third-parties. We did not meet this target this year and we are re-doubling our efforts to meet this target in 2025.
We have a 2025 target of 98% 3TG traceability and conflict free status to smelter level in our supply chain as well as conflict free status of the smelters. Extended due diligence and conflict free status of cobalt, mica, aluminum and copper. As of 2024 we have achieved 87% traceability to the smelter level in our supply chain as well as conflict-free status of the smelters (6% basis points improvement from 2023). We have also extended and conducted due diligence for cobalt, mica, aluminum and copper. The work continues to close the remaining 11% gap to reach the target in 2025.
Overview of Nokia supplier requirements
EcoVadis, the world’s largest provider of business sustainability ratings monitors sustainability in global supply chains. We ask our key suppliers for their EcoVadis scorecard rating and are proud of our own where EcoVadis has again ranked Nokia in the top 1% globally in 2024.
Our materiality analysis and Enterprise Risk Management help identify potential supply chain risks. We carry out more in-depth analyses to determine all supply chain risks through our dedicated Supplier Sustainability Risk dashboard where we look at various sustainability risks, commodity risks and more on a supplier location level. The outcomes are included in our category strategies. We review category strategies annually with our purchasing category leads. Failing to meet established sustainability requirements will block a supplier from being promoted, for example, from “restricted” to “allowed”, or to “preferred” status. We also maintain and regularly update a corporate responsibility risk map of our suppliers.
Our key supplier-related monitoring, assessment and auditing activities include an on-site corporate responsibility audit program, EcoVadis sustainability assessments, our in-house health and safety Supplier Maturity Assessment (SMA), and the CDP Supply Chain Climate Change and Supply Chain Water Security assessments.
Our in-depth audits are aligned with SA8000 methodology, and we implement a range of audits and assessments including:
- Our general supplier requirement audits
- Corporate responsibility in-depth audits
- Supplier Health & Safety Maturity assessments
- Conflict Minerals Audits
- Assessment tools such as EcoVadis and CDP
Highlights related to audits
- 606 supplier audits conducted in 18 countries
- 420 improvement recommendations made, which were addressed through corrective actions.
Awareness raising and climate data collection
Every year, we host the Nokia Supplier Climate webinar where we share our expectations, 2030 targets and good practices coming from different stakeholders within Nokia. We also send out an annual climate assessment questionnaire via CDP to nearly 600 suppliers. For further information, you can read more in the supply chain section of our Environment webpage.
Combatting modern slavery, forced labor and labor migration risks
Modern slavery and forced labor of all kinds remain a challenge for all countries and supply chains.
We have robust audit and assessment processes and procedures in place. We continue to raise awareness of modern slavery, forced labor and labor migration through workshops and training with suppliers to ensure good labor practices and inclusion and diversity in their operations. We do not tolerate slavery, servitude, human trafficking or forced or compulsory labor in our own operations or in our supply chain. In June 2024 we published our annual Modern Slavery Statement.
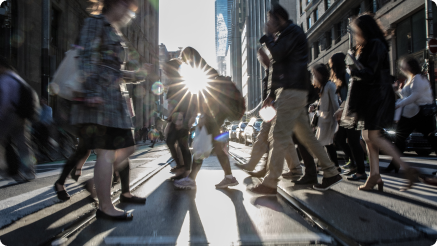
Materials traceability and conflict minerals
We aim to contribute to a long-term solution to the issue of minerals sourcing that ensures responsible and conflict-free sourcing via legitimate trade that brings sustainable improvements in those countries where the risks are greatest. We demand that our suppliers commit to sourcing these key materials from environmentally and socially responsible sources. Our due-diligence approach is aligned with the OECD Due Diligence Guidance for Responsible Supply Chains of Minerals. We are part of the RMI program under RBA and have released a Conflict Minerals Report every year since 2013.
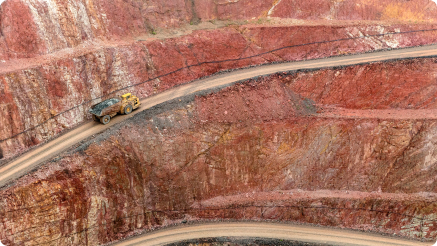
Water in our supply chain
We address supplier categories where water may be a material risk through a water assessment program that includes awareness raising, annual data collection, target setting and follow-up. In 2024, our manufacturing suppliers completed the CDP Water Security assessment, representing 52% of our total supplier spend. Out of the participating suppliers, 80% had undertaken a water-related risk assessment for their direct operations and identified actual water-related risks in their operations such as flooding or increased water stress or scarcity, potentially resulting in the reduction or disruption in production capacity or increased operating costs. 48% of suppliers had structured targets related to water consumption, discharge or withdrawals. Targets were mostly related to internal efficiencies rather than being contextual.
Supplier learning and capability building
In addition to auditing and assessing our supplier performance across ESG topics, we also put significant effort into our supplier capability building in collaboration with a range of partners (see partners section) as well as directly. Our sustainable supply chain team has hundreds of follow up sessions with suppliers around their performance improvement. We also conduct and deliver training webinars online and onsite including topics such as diversity and inclusion, modern slavery, responsible minerals sourcing, climate change, health and safety, and ethical business practices.
Health and safety supplier maturity assessment (SMA)
Health and safety in our supply chain is a non-negotiable – it is our priority. Many of our subcontractors work at height with electricity, and they need to drive long distances as part of their work on our behalf.
We have set stringent KPIs related to our health and safety Supplier Maturity Assessment (SMA), which is our in-house-developed assessment. This assessment helps to ensure that contractors know Nokia’s health and safety requirements and are capable of delivering work safely on our behalf. It also helps ensure that projects have risk-mitigation procedures and controls in place. We also conduct supplier training to provide awareness of potential dangers related to their work and to ensure that the correct safety equipment is used as required.
At the end of 2024, 98% of high-risk activity services suppliers were covered by our SMA. 98% of assessed suppliers met health and safety “Compliant Supplier” status (score of 3 or more out of 5). Any supplier not meeting our health and safety requirements was, in the case of a new supplier, blocked from qualification, and in the case of an existing supplier was to be phased out or required a thorough improvement where we had no alternative supplier.
Recognizing supplier achievements
Sustainability is one category in our annual Supplier Diamond Awards alongside the Quality Award and the Innovation Award. The Supplier Diamond Awards are Nokia’s annual recognition program to reward supplier excellence across several categories including sustainability. Suppliers present their cases in front of expert juries and are recognized at our annual supplier event, in the presence of Nokia top leadership.
Previous winners in the sustainability category include one of the leaders in sustainable semiconductor manufacturing – examining the decarbonization of its own operations, establishing a net-zero target for 2040 and collaborating with Nokia to reduce the emissions of our products.
Industry collaboration
Nokia is very active in various industry forums around sustainability issues. Below is a list of organizations that we collaborate with around responsible sourcing and supply chain topics.
Responsible Business Alliance (RBA)
Nokia is a member of the RBA, a coalition of the world’s leading companies working together to improve efficiency and social, ethical, and environmental responsibility in the global supply chain. As a member we endorse the role that industry collaboration plays in improving challenging issues. We participate in various networks and working groups within RBA, such as the Responsible Minerals Initiative (RMI). We support the mission of the Alliance and have adopted the RBA Code of Conduct as the basis for the requirements we place on our suppliers, further supplemented by Nokia own supplier requirements.
Sourcing and supply chain issues are ever more complex and we believe can be addressed more effectively via industry collaboration and shared efforts that are built on common working groups and understanding. We also look forward to contributing with our years of experience in sustainability and responsible sourcing issues worldwide.
CDP (Climate and Water)
Collaboration on annual assessment of supplier climate emissions, water use and supplier learning and capability building on these topics.
EcoVadis
Collaboration on supplier assessment, improvement, and training across sustainability portfolio including labour, environment, ethics and supply chain.
Joint Audit Cooperation
Nokia collaborates with our telecom customer network JAC on supplier audits, corrective actions and capability building.
Public-Private Alliance for Responsible Minerals Trade – RESOLVE
For upstream engagement around responsible minerals trade we have continued our work with the Public-Private Alliance, contributing to the development of in-region programs for responsible minerals trade.
Public-Private Alliance for Responsible Minerals Trade - RESOLVE
Sourcing and supply chain issues are ever more complex and we believe can be addressed more effectively via industry collaboration and shared efforts that are built on common working groups and understanding. We also look forward to contributing with our years of experience in sustainability and responsible sourcing issues worldwide.
Long term targets and commitments
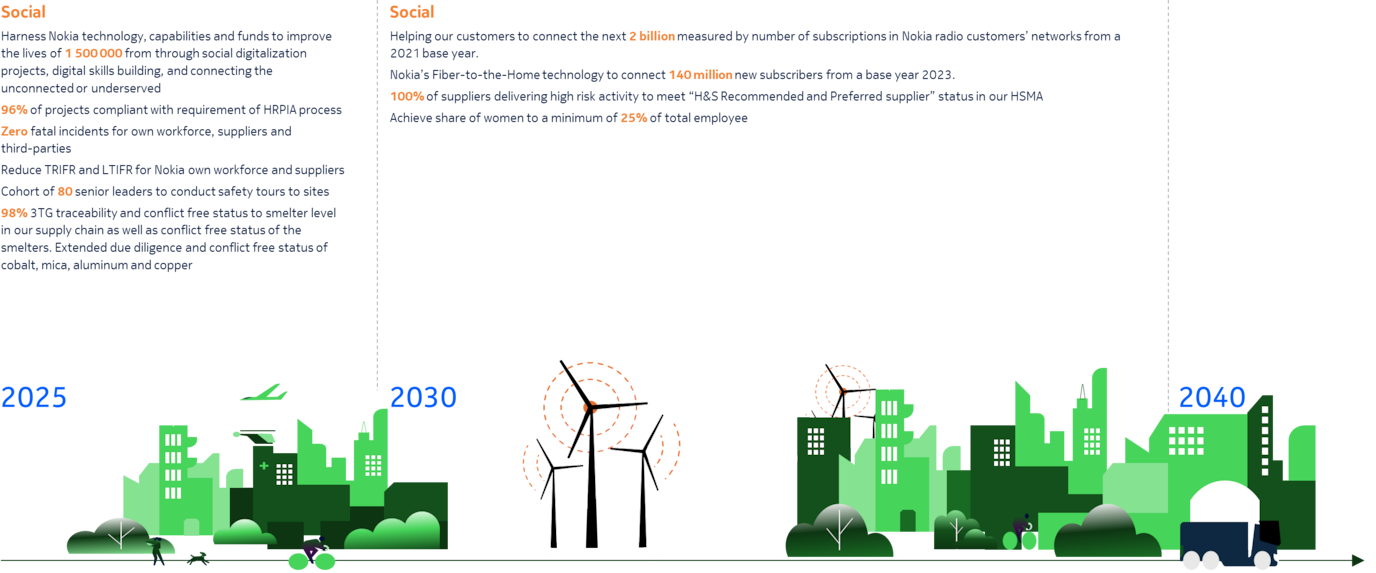