Autonomous haulage: welcome to the future of mining
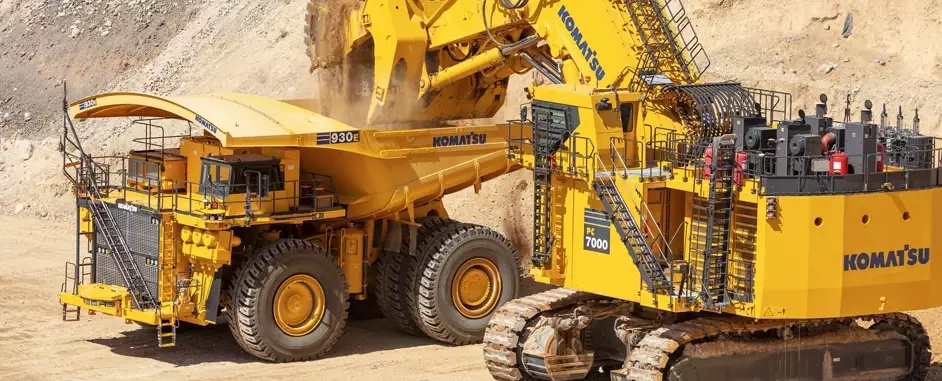
Before the summer holidays, I had the pleasure to co-present a webinar with our partner Komatsu.
You may already have come across the Komatsu logo on a bulldozer or on a forklift truck. But, believe me, these are only some the smaller vehicles the company builds. Komatsu is one of the big equipment suppliers of the mining industry. And when I say big, I mean really biiig: think of giant shovels, excavators and dump trucks. Komatsu’s largest off-road haul trucks run on 3.8-meter (150 inch) tires and they can transport up to 360 tonnes of ore.
The company is also a pioneer in mining automation – they launched their first computerized dispatch system in 1980 – and today, with 250 autonomous trucks in operation worldwide, they are a market leader in Autonomous Haulage Systems (AHS) – their FrontRunner AHS system recently passed the three billion tonne mark.
As mining companies are pursuing a full automation strategy without human intervention (aka Level 9 automation), where all manually operated equipment, including diggers, ore haulers, crushers and trains will eventually be replaced with their autonomous counterparts. Remote operations will further supplement automation, allowing personnel to monitor automated processes and operate machinery at a distance using virtual telepresence.
Almost all our Nokia mining customers are looking at remote and autonomous operations as the obvious use case for business transformation. AHS technology has already delivered proven benefits in productivity, durability and safety in an array of mining environments. In 13 years of AHS operation, Komatsu has recorded zero system related accidents or injuries. As there is no more no need to stop for shift changes or crib breaks, they enable increased productivity and production.
An interesting use case for AHS, as shown on the image above (photo courtesy of Komatsu), is hang time reduction. ‘Hang time’ is the amount of time that a shovel or a digging unit might hang with a full bucket waiting to dump its ore in the truck. With an automated system in place, a shovel can reach zero hang time as the truck navigates to the spot point automatically, without the shovel needing to hang as a visual indicator. At a rate of 18 loads per hour and 20 hours per day, automated operations have shown to add more than 500 extra hours of shovel capacity and a huge productivity increase of more than 2 million tons per year.
Providing the robust, predictable and secure wireless connectivity that’s so essential for extreme automation, including the operation of AHS systems, is however beyond the capabilities of today’s enterprise wireless technologies, like Wi-Fi. Private 4.9G/LTE and 5G wireless networks provide the capacity and coverage and reliable, low-latency communications to enable upstream video transmission, collecting of sensor data and remote control of vehicles and machines.
In January 2019, Komatsu announced the mining industry’s first Autonomous Haulage System (AHS) running on Nokia Industrial-Grade Private Wireless technology in commercial operation, making way for ultra-high system availability and reliability, while adhering to Komatsu’s renowned safety standards. In the meantime, more than half of Komatsu’s production sites in North America, Latin America and Australia are on Nokia industrial-grade private wireless.
During the webinar, David Haukeness, Komatsu’s product manager for AHS, explained why a reliable, service-aware wireless broadband network has been instrumental to make AHS systems a reality and why the company is partnering with Nokia on their proving grounds in Arizona.
David told us that LTE’s increased network reliability has allowed Komatsu to focus resources on application development and customer value instead of always having to ask: “is this caused by the network?” Working with Nokia has enabled them to meet customer demand, letting their mining customers operate safer, increase production by up to 12% and run data collection and analytics in parallel with mission critical traffic on a single network.
Nokia and Komatsu are committed to continuing our joint journey to take mining automation to the next level – moving beyond connectivity and further developing 4.9G/LTE and 5G network-enabled solutions that will create ever-safer, more productive and efficient mines.
If you’re looking for more details and proof points of the above, you may replay our “Making Autonomous Haulage Systems a reality” webinar.