Does lean have a limit? Why resilience matters as much as efficiency in your supply chain
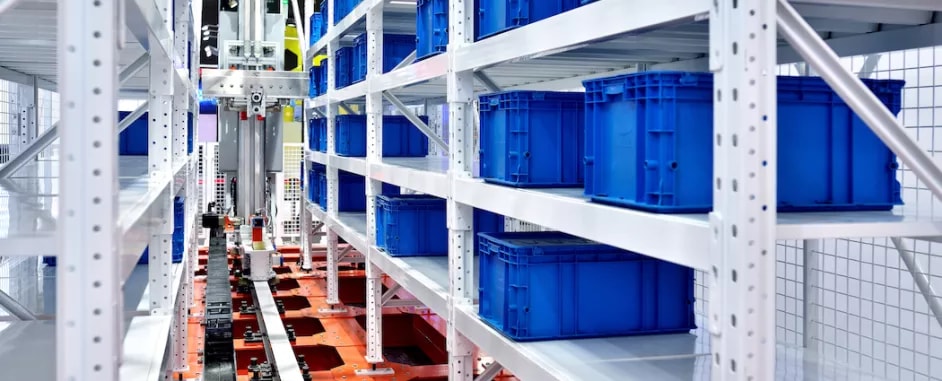
In struggling to deal with the disruptions caused by COVID-19, many supply chain organizations found that years of cost optimization and sourcing options had stripped them of much-needed flexibility. It turns out that just-in-time systems with almost no buffer are great when conditions are predictable but likely to grind to a halt when they aren’t. Automation and intelligence are key to providing the on-the-fly adaptability modern supply chains need, and warehouses are among the first places organizations may want to look to start reaping the benefits.
It’s possible to be too lean
Over the last several years, cost optimization has become the holy grail for supply chain organizations: trimming every last bit of fat out of processes for maximum efficiency. Years of fairly predictable, repeating business cycles — peak sales at holidays dips right after — made it possible to order and deliver nearly exact quantities of raw materials, components, and finished goods with almost zero standing inventory and in record time. And supply chains became reliant on sourcing from a limited pool of suppliers, preferring to simplify their business operations to a small network of vendors.
But that highly efficient process ran the risk of turning downright brittle if those patterns suddenly couldn’t be counted on, and with serious consequences. According to McKinsey, “a single prolonged production-only shock” could cut most companies’ annual EBITDA by as much as half — and even more if distribution channels were implicated.
COVID-19 has definitely been a “prolonged shock”, and it has thrown supply chain vulnerability harshly into the spotlight. According to EY and Fortune, 94% of Fortune 1000 companies have experienced supply chain disruptions as a result of the pandemic. Factory shutdowns and grounded transportation networks have caused production and delivery delays. Some organizations started stockpiling raw materials, which has introduced further capacity pressures.
At the same time, consumers started “panic buying” toilet paper and other goods, and demand for essential supplies such as personal protective equipment and hygiene products skyrocketed, exhausting the normal inventory that did exist. Sudden lifestyle shifts also drove surging demand for a wide and unpredictable range of products from birdseed to baking supplies to fitness gear.
With little buffer to ride out supply delays and no other suppliers available to fill the gap, it quickly became impossible for companies to meet demand, causing shortages and disruptions all along the supply chain.
A new reality, new rules
Supply chain operators have also had to adjust rapidly to new regulations for worker safety, facility sanitization, and public health protocols due to the pandemic. Tried-and-true ways of clearing out a backlog — for example, by boosting headcount with temporary staff — weren’t available because of physical distancing restrictions.
Stringent facility cleaning requirements have further strained resource capacity and are not financially sustainable over the long term. Companies who lacked the agility to quickly adapt processes to comply with recommended health protocols, found themselves facing substantially lower productivity, complete shutdowns, or – in the worst cases – disease outbreak.
Companies need new strategies to improve the resilience of their supply chains while keeping operational costs down — the strategies of Supply Chain 4.0.
Shifting toward Supply Chain 4.0
Transforming to Supply Chain 4.0 is going to take time and incremental steps. Logistics warehouses provide a convenient and practical starting point for quick gains by deploying new technologies and reimagining material and business process workflows — with robotics and intelligently automated processes.
Specifically, supply chain operators can start by implementing three key enablers:
- Pervasive high-bandwidth connectivity and scalability
Warehouses can be outfitted relatively quickly with high-performing networks that extend to every corner of the operation and communicate with other warehouse locations.
- Massive Internet of Things (IoT) adoption and integration
With the network in place, all the devices, machines, and people in the warehouse can be connected to it and each other, enabling robots and other automated systems to move around, locate items and carry out tasks including packing, assembly, inventory, and cleaning. Key applications could include wireless HD video feeds, augmented and virtual reality tools, autonomous guided vehicles, and more.
- Predictive and prescriptive analytics
Data analytics-based systems can be implemented to monitor worker safety, predict supply chain-affecting events, assess alternate flows, and proactively monitor system maintenance needs. For example, automatic worker temperature checks can identify workers running a fever so they can receive appropriate medical intervention and those nearby can also be proactively tested to help contain potential outbreaks. Asset management systems can predict maintenance needs and automatically or prescriptively shift flows to ensure optimum system performance with little to no disruption. At the same time, predictive systems can assess the impact on the supply chain and leverage digital twins to plan, test, and propose measures to ensure continuity.
By moving toward greater automation and the use of robotics, it is estimated that warehouse operators can save 70% in overall operating costs while continuing to meet customer service needs and achieving greater operational flexibility.
Build resilience and optimize cost
At Nokia, we’ve spent years creating Supply Chain 4.0 solutions that are purpose-built for real-world logistics environments, with a comprehensive, end-to-end portfolio of easy-to-deploy wireless solutions. Our supply chain/logistics automation products and solutions are purpose-built for supporting mission-critical operations but are offered in scalable options with simple installation, set-up, and management, all in a compact footprint. Our solutions have been developed in close collaboration with a wide ecosystem of partners — from supply chain organizations to robotics companies — to ensure all the parts inter-work together to deliver real Supply Chain 4.0 benefits.
Strategists and innovators in the logistics industry have been talking about Supply Chain 4.0 for years, but mostly as a “someday” project. The urgencies of COVID-19 have highlighted the need to accelerate the implementation of Supply Chain 4.0 automation - now. Smart automation can radically reduce delivery times and waste all along the supply chain. Real-time transparency makes it possible to adapt fast to changing supply and demand conditions, providing flexibility and resilience without sacrificing cost optimization.
Want to know more?
Please join our information-packed webinar, 5G, and private wireless networks to automate and digitalize your supply chain. Our supply chain technology advisors are here to help you design the right solutions to meet your challenges.
For more information on Nokia solutons for Supply Chain and Logistics operations, visit our website.