How a near-miss forklift accident is helping architect the future of industrial communications
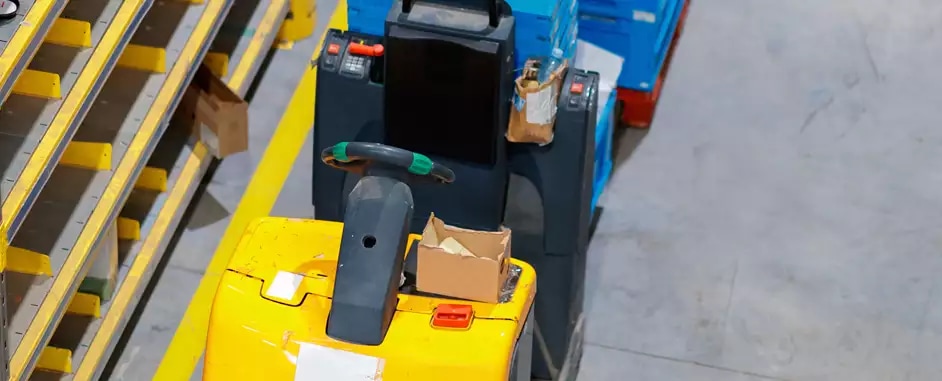
On October 22, 2020, a forklift accident was narrowly averted at a warehouse in Germany. Fortunately, no one was hurt and no damage was done thanks to the combination of situational awareness sensors in the next-generation forklift and the facility’s private wireless network. The near-miss was a practical use-case demonstration, part of an event marking the culmination of three years’ work to develop an easily deployable, comprehensive reference architecture for industrial communications — and Nokia was at the heart of the action.
Partners in bringing Industry 4.0 to life
The U.S. Occupational Safety & Health Administration estimates that forklifts account for 61,800 minor injuries, 34,900 serious injuries, and 85 deaths each year — with the majority happening in the manufacturing sector. Developing solutions to reduce those kinds of accidents was just one of many concerns for the Industrial Communications for Factories (IC4F) consortium, which is exploring ways to take solutions and technologies used in public communications networks and apply them to industrial contexts.
IC4F was created in 2017 by Germany’s Federal Ministry for Economic Affairs and Energy to develop and demonstrate secure, robust, real-time communications solutions that will improve automation and digitalization in manufacturing, supply chain and logistics. Nokia has been an IC4F member from the start, along with 14 other industry, academic and ICT sector partners including Bosch, Siemens, Deutsche Telekom and the Fraunhofer Society.
The output of this cross-sector collaboration was on display in October at the Hamburg facility of intralogistics company STILL, including a live demo of “truck-to-X” communications between forklifts and the warehouse’s digital environment. The presenters showed how STILL’s smart warehouse doors opened automatically when the connected forklifts approached — but only if embedded sensors, communicating with a “digital twin” (a virtual model of assets and infrastructure in the warehouse) programmed with the forklift’s precise dimensions, confirmed that the vehicle would fit through. If not, the forklift’s drive control was accessed remotely and the driver was warned. The potential accident was averted — along with what could have been costly damage to doors and vehicles.
Other industrial use cases demonstrated at the event included “crowdsourced” asset tracking, showing how asset positions could be monitored in near-real time using wireless devices in forklifts and low-energy Bluetooth beacons located every 10 to 20 meters throughout the warehouse. Also featured was an industrial edge cloud, which securely and compliantly hosted multiple components on a shared communications and computing infrastructure.
The next step? To make these kinds of applications accessible to smart warehouses and smart factories all over the world through an easy-to-use toolkit.
The building blocks for Industry 4.0 and smart factories
The solutions and research presented in Hamburg were all driven by IC4F’s main goal: to develop and validate a reference architecture and toolkit so any manufacturing or logistics company can easily choose the most suitable technologies for their own secure, reliable, comprehensive communications and computing infrastructure.
The IC4F industrial reference architecture (iRefA) provides a structured, modular methodology — verified against Industry 4.0 requirements and use cases — that simplifies the process of designing, modeling and implementing enterprise ICT architectures. Its web-based visual toolkit includes catalogs of predefined architecture and solution “building blocks” (or templates) and a repository of validated, mature architecture patterns. It also features built-in user guidance, greatly accelerating the deployment of Industry 4.0 solutions from the shop floor to a facility’s control and execution functions.
The toolkit is based on an open, cross-domain architecture that covers the technology, information, business and security layers. It can also be extended in a modular way to easily incorporate new applications and communications technologies as they emerge in the future.
Nokia played a central role in developing and validating the iRefA. Our mobile network solutions team provided the private wireless campus network and localization technologies at the heart of the Hamburg demonstration projects — a “hidden champion” working behind the scenes to make it all possible. Nokia Bell Labs also researched access, compute and security aspects of 3GPP/IEC/IEEE standardization, including cybersecurity and the use of 5G versus Wi-Fi for time-sensitive communications, to determine how typical ICT platforms will need to be adjusted to meet today’s increasingly demanding industrial requirements.
Beyond the smart factory
A simple, easy-to-use industrial communications reference architecture matters not just from a technical perspective but a business perspective as well. With iRefA, manufacturing, supply chain and logistics organizations get a “plug and produce” approach to wireless communications, automation, and digitalization, without getting bogged down in extensive network architecture testing and validation processes — allowing them to get to market with Industry 4.0 solutions much faster.
With iRefA agreed to by all IC4F project partners, we at Nokia are now developing industrial communications products and solutions across our entire enterprise portfolio that comply with its requirements and approach, even beyond manufacturing, with a particularly close look at applications for industrial-grade 5G private wireless networks.
For more on this topic, look for an upcoming blog about the 5G innovations uncovered at the second IC4F demonstration event that was held in November at Arena2036 and the potential they bring for the smart manufacturing era.
Click here to learn more about Nokia solutions for manufacturing, supply chain and logistics.