Plan, simulate, optimize: creating value with digital twins
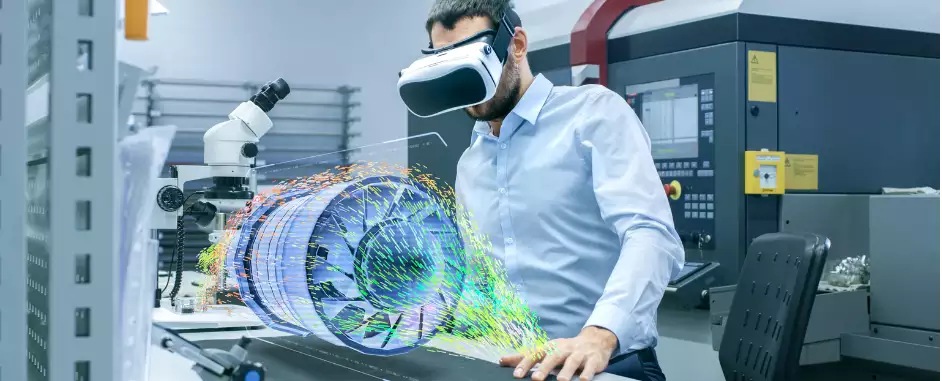
Digital and virtual twins are one of the major technology trends in telecommunications and industry, especially in the context of 5G campus networks. We examine where businesses can use digital twins, when an investment pays off, what to consider during the planning stage, and the role played by connectivity.
A digital or virtual twin is one of the most important application cases available for companies to automate their processes—whether in the production, logistics, automotive, or energy industry. It involves creating a digital model, or twin, of one or more industrial processes, such as those in a factory, logistics center, or power plant. In addition to providing a tool for monitoring process steps in real time, companies also use these virtual copies to better plan, simulate, and optimize process results. A 5G campus network provides the reliable, secure, and high-performance connectivity required for the digital or virtual twin to access data from machines, robots, or workers.
Planning 5G campus networks
A digital twin can also be used to plan a 5G campus network. This approach enables the installation scenario, hardware components used, and configuration to be optimized in advance without having to compromise on connectivity in the production hall at a later stage. In turn, this makes it easier for industrial companies to implement a suitable wireless network, which is essential for modernizing production. It also reduces the associated installation costs and time. According to an analysis by McKinsey in late 2022, a digital twin can increase profits by up to 10 percent, coupled with a 50 percent reduction in time to market and a 25 percent increase in product quality.
Virtual twin – taking it one step further
A virtual twin is often considered an extension of the digital twin. Whereas a digital twin visualizes process data and enables simulations to be run using actual data for optimization purposes, a virtual twin goes one step further. In addition to simulating the actual process, it also considers the entire value and supply chain, together with its associated assets, and enables processes to be tracked from end to end. This in turn brings further improvements, such as increased agility in production, faster decision-making processes, or a competitive advantage in the market through innovation. A virtual twin also enables users to immerse themselves in a realistic 3D model using augmented reality technology. This environment can be used to analyze data about the target/actual process in detail, conduct virtual meetings about optimization, and view simulation results virtually. Software solutions, such as those provided by Dassault Systems, create a new, realistic simulation experience for factory and operations managers that provides optimized data visualization, tolerance comparisons, and opportunities to share knowledge and collaborate within teams.
From analyzing the past to predicting the future
The use of such software allows the virtual twin to be used at different levels of the organization and at different times in the production cycle. This starts with planning a 5G campus network for the production site and the associated network optimization and certification, which can be accelerated using the virtual twin. Once the infrastructure is operational, the entire value chain can be mapped and optimized. This includes performing an automated inventory of the resources, goods produced, or required storage space. Companies can also use the factory's virtual twin to optimize the production environment and to control, synchronize, and manage manufacturing processes. In addition, suppliers and supply channels can be integrated to provide a holistic overview. In short, a digital twin looks to the past and describes the present, while a virtual twin enables predictions to be made about the future.
5G campus network or 4G/LTE?
A digital or virtual twin can collect and consolidate data across different network types. Machines, robots, sensors, and cameras in factory or warehouse buildings transmit their data to the virtual twin platform via a cable. Mobile logistics vehicles, wireless tablets for machine control, sensors on personal protection equipment worn by factory workers, and cameras on drones used to monitor and inspect the company premises all use mobile networks to provide their data to the virtual twin. The choice between 4G/LTE and 5G depends on the application. Although 4G/LTE is suitable for use with sensors and simple machine monitoring, the high performance and safety certifications offered by 5G technology are required for sophisticated high-definition video signals or the safe control of robots. The availability of the 4G/5G spectrum at the national level also determines which technology can be used to operate a campus network.
On the path to a long-term operational concept
A 5G campus network project usually starts with a proof of concept (PoC). This involves setting up a small campus network with a limited number of antennas and a decentralized control unit, referred to as the edge core, directly on the company premises, which enables initial experience to be gained of the above-mentioned application cases, the 5G technology, and the resulting process changes. This is necessary because campus networks are just one component of Industry 4.0 digitization. Network equipment suppliers like Nokia and its partner companies can take over the planning and installation of such a campus network, place it into operation, and subsequently hand it over to local IT managers or operate it as a managed service, depending on customer requirements. The lead time for such a pilot project is usually six to nine months, depending on the project scope and hardware delivery times. Over the subsequent twelve to 18 months, the network will often be extended to further halls or areas and the campus network will be integrated into productive, critical industrial processes, followed by a concept for long-term support and operation. When setting up the technical equipment, it is also necessary to take into account country-specific frequencies, perform precise network and capacity planning, and integrate with the existing IT infrastructure. Companies such as Nokia and Dassault Systems support this digital transformation from start to finish.
Return on investment
The return on investment of 5G campus networks is highly dependent on efficiency gains. It is also recommended to extend the 5G campus network gradually across multiple scenarios to optimize the return on investment, and to start with one initial PoC network followed by larger roll-out phases. To put this in concrete figures, ABI Research conducted two case studies in collaboration with Nokia. By introducing Industry 4.0, a German car manufacturer was able to achieve cost savings of 6.7 percent ($530 million) within a five-year period. And the savings at a Japanese consumer electronics manufacturer amounted to 8.9 percent ($220 million), also within five years. In addition to cost savings, a campus network enables greater flexibility at the production site while simultaneously ensuring high data security.
H2: On top of the network
5G private wireless networks serve as a technical enabler for a variety of applications — from autonomous robots and industrial trucks to connected workers with tablets and intelligent workwear through to drone cameras and human-machine control. In addition to the actual campus network consisting of antennas and a distributed control unit, the efficiency, performance, and security advantages afforded by 5G also require the use of terminals and applications. The terminals enable machines, robots, tablets, and sensors to be connected to the 5G campus network using a dongle, industrial router, or a 5G-capable smartphone or tablet ruggedized for industrial use. The applications, such as the Dassault Systems platform for digital twins, receive the transmitted data and make it available for industrial use. Another key element is system integration, which combines the 5G network and new use cases with existing ERP, MES, and IT systems.
Fast data processing is crucial in Industry 4.0
One of the strengths of Industry 4.0 is the ability to analyze the collected data and thus optimize processes. To enable this, applications and software must be made available that can evaluate data in real time. This requires data processing with the shortest possible delay using on-site computing capacities, referred to as the mobile edge cloud. Fast data processing is also important for interacting with robots without interruptions. To take full advantage of the virtual twin, companies can anticipate the future when planning and operating their production facilities. They do this by combining structural data models and virtual twins of individual network or production components into a consolidated virtual twin and evaluating all available information. The potential of virtual twins in Industry 4.0 is particularly diverse in this regard.