Sharpening the Edge for Industry 4.0
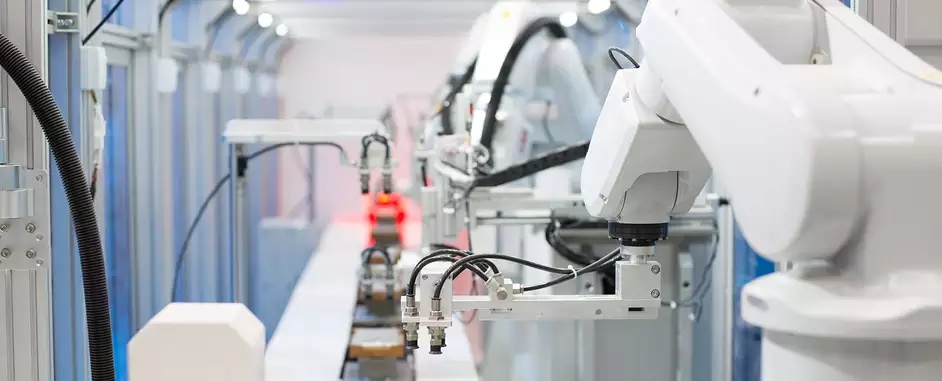
Circa 2020, COVID-19 raised the perfect storm for many industries and enterprises as they were forced to deal with a veritable ‘double whammy’ of supply-shock and demand-shock. To make matters worse, strict ‘lockdowns’ across various countries meant that factories and production units across the world had to make do with a fledgling workforce that could just about keep the lights on.
Adapt or die – the writing was on the wall for those who had, till then, kept Industry 4.0 digitalization plans on slow-burn since they were confident that their established processes would help them through any market turns. A priority candidate identified for transformation was the Operational Technology (OT) environment. OT is critical because it enables enterprises to monitor and control physical processes, systems, devices and infrastructure in production environments. In other words, it gives enterprises the means to control the physical with the digital. Digitalization at scale across the OT environment enables agile production and the ability to dynamically adapt operations to changing situations.
Enabling agile production through OT digitalization
Let’s take an example from Nokia’s 5G Oulu factory - recognized by the World Economic Forum as an "Advanced 4th Industrial Revolution Lighthouse". One well known use case implemented at Oulu is the application of video analytics for quality assurance and control. While important in its ability to ‘left-shift’ quality, Video Analytics is just one part of the integrated digitalization approach that makes the shopfloor truly agile.
4K cameras on the assembly line can wirelessly stream data to the local edge cloud where compute extensive analytics are performed in real time. Anomalies detected trigger a call and notification to the technician responsible for that particular assembly line while also sending a message to the master manufacturing execution system (MES) to modify scheduling and shift operations to a different fully functioning assembly line. AGV’s carrying raw materials are rerouted to the new assembly line and production continues.
Data processing shifts to the Edge
The Edge Cloud plays a critical role in integrated OT digitalization - it provides the compute, storage and networking infrastructure, hosts all the industrial applications, receives data from a variety of IoT devices through industrial private wireless connectivity, processes the data and workloads generated, provides AI driven insights, facilitates app to app communications and automated workflows, while sharing critical updates with master systems like the MES. All in near real time.
Today, just 10 percent of enterprise data is processed outside a centralized data center or cloud. But enterprise systems are generating data faster and in bigger volumes, and real-time analysis and automation are becoming more important. It’s no longer efficient to stream all data to a centralized cloud. Gartner predicts that edge computing systems will process and analyze 75 percent of data by 2025.
Key considerations when selecting an Industrial Edge solution
Large enterprises have embraced edge computing, but many believe it’s essential to retain control over their data. As a result, on-premises edge architectures remain the most popular choice for enterprises who value data sovereignty. Mobile Experts estimates that as many as 21,000 on-premises edge clouds and data centers will be operational by 2025.
Not all on-premise edge solutions are built equal. A disruption in mission critical OT operations can have major consequences – ranging from total shutdown of assembly lines in a production environment, to environmental impact and even injury and loss of life for personnel. Failure is not an option. The Industrial Edge must be designed to provide the assured high performance, extreme resilience and security hardening demanded by mission-critical industrial OT environments.
The Industrial Edge should also have features and capabilities extending beyond traditional ‘infrastructure-only’ Edge, to simplify the deployment and management of end to end Industrial IoT (IIoT) based industrial automation use cases. Gartner estimates that nearly 15 billion IoT devices will connect to enterprise networks by 2029.
As IT budgets get strained due to accelerated digitalization initiatives, many enterprise and industrial customers are looking for edge solutions with lower upfront investments and a more manageable subscription fee. Flexible consumption-based pricing models will help these customers accelerate return-on-investment (ROI) from their edge digitalization spends.
A mission-critical Industrial Edge solution that accelerates OT digitalization
It is essential that an Industrial Edge solution is ‘mission-critical’ by design – bringing high performance to run a variety of demanding workloads, while providing extreme resilience through features like high availability and geo-redundancy. It also needs to be security hardened – ensuring all data communication only happens over secure protocols like TLS.
Equally important is that the Industrial Edge solution should be more than just ‘infrastructure’ – offering a rich set of IIoT capabilities like industrial connectors, click to deploy industrial applications, device and application management, to simplify and speed up the industrial OT digitalization journey. Ecosystem neutrality is critical here – giving customers the power to choose and deploy the latest innovations from webscale and industrial cloud ecosystems.
Solutions like Nokia’s new MX Industrial Edge are addressing these needs of asset intensive industries by offering a fully integrated mission critical edge solution that combines the simplicity and agility of an edge-as-a-service model with a resilient, secure and high-performance edge architecture. So, now’s the right time to ‘gain an Edge’ and usher in the Industry 4.0 revolution!
Visit our solution web page to find out more about how the MX Industrial Edge can help you digitalize your OT and bring Industry 4.0 to your production environment.