The four key takeaways from chemical industry leaders on their digitalization journey
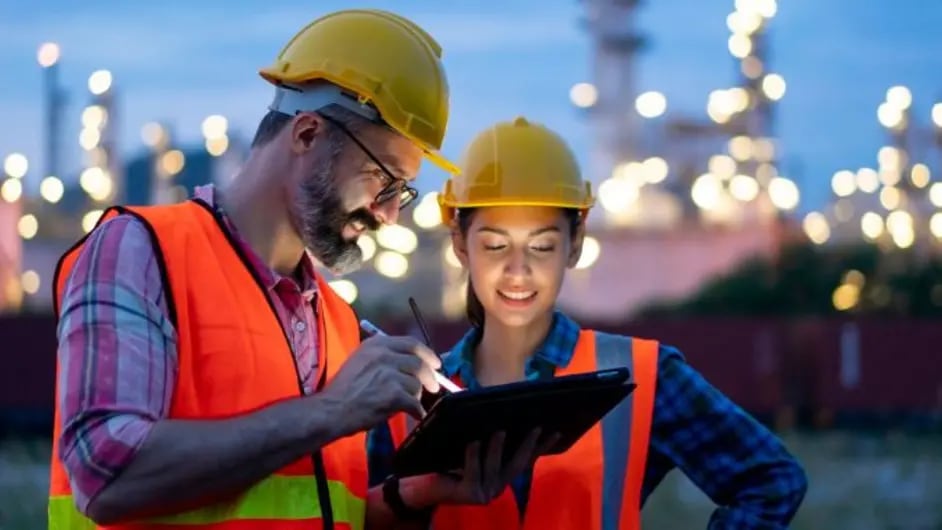
We recently interviewed leaders in the chemicals and plastics industry to understand what digital transformation means to them. Having long employed digital technologies within their operations, the current focus of their digitalization efforts is on using Industry 4.0 technologies, like IoT, analytics, and digital twins to capture data and also using the power of AI and machine learning to optimize their operations. We conducted in-depth interviews across Europe and the US with C-suite executives, process engineers, supply chain managers and digital transformation engineers to uncover some key trends.
The high-level takeaways from the interviews are that everyone in the industry is going digital. The largest chemical companies are well down the track, while small and medium companies aren’t as advanced, and many wish they’d started sooner. They see digitalization as a means to, make their businesses more efficient, eliminate human error, make better decisions faster, and improve the security, safety, and sustainability of their operations.
Digging down into those high-level ideas, the interviews uncovered some interesting trends in which private wireless can provide solutions to some common challenges in the chemical and plastics industry.
1. End-to-end optimization means removing the silos
Most of the individual processes within a chemical or plastics factory today use digital measurement and control for managing their production line and have been doing so for decades. The systems tend to be purpose-designed and built with proprietary hardware and software, including data formats that are incompatible with neighboring processes and systems. As a result, companies have a lot of disconnected data lakes with little or no sharing between them. Removing the silos between legacy systems is expensive and additional custom integration means upgrades become more complex.
According to the study, this poses a number of challenges. For a factory manager responsible for optimizing overall operations, this means that on a day-to-day level, there is a lot more paperwork, no real-time dashboards for the operation as a whole, and analysis is complex and time-consuming. This slows down decision-making, introduces more scope for human error, and makes management reactive instead of proactive.
2. Make sense of the data firehose
Meanwhile, IoT technologies are making it possible for companies to collect data that wasn’t available before. Leveraging these new technologies is where most SMEs are today. They are deploying condition monitoring sensors to measure pressure, temperature, flow and levels for processes that weren’t measured before. One interviewee described IoT as enabling them to capture “1,000 times more information” than in the past. When this information is analyzed and applied, the results are greater safety, better quality control, less waste and more efficient energy use.
The largest players in the industry, have already implemented IoT technologies and are actively using the information today. The challenge for them is to make it useful in real-time. Many already use digital twins or automated models that run alongside actual processes. By running the model in real-time, they are not only able to see what the process is currently doing but can simulate where it is going or could go. This predictive ability enables them to control quality, adjust resources and save energy and avoid potentially dangerous outcomes.
The ultimate objective, which few of them have achieved yet, is to implement AI and machine learning (AI/ML) analytics to fully optimize their processes. The main roadblock is still lacking good quality real-time data in some areas of their operations. This issue isn’t specific to the chemical industry as most industrial sectors now recognize that having good quality, proprietary data may well be the single most important competitive advantage in the era of AI/ML. This puts even more emphasis on collecting, storing, processing and communicating data from all aspects of the operation.
3. The connected worker replaces the control room
One interviewee shared an anecdote, when in one project, he asked the people building the plant where the control room was going to be. They replied "We don’t have one. Our control room is wherever the operator is. Each operator would have a device to see exactly what was happening with each operation in real-time".
As with many industries in developed countries today, the demographics of an aging population are posing operational challenges. On the most basic level, companies are facing recruitment challenges as the baby boomers retire. As companies look to do more with less, automation is a high priority.
It is not just an issue of replacing workers, but the knowledge management issues posed by the loss of senior engineers. Companies need to do a better job of capturing what senior people know and transmitting it to new recruits. Virtual reality applications for training and augmented reality applications for supplementing workers’ knowledge on the floor are seen as an exciting area to explore by all companies.
The new generation of recruits expect companies to be digital and to attract people, digital tools to perform their jobs can become a competitive advantage. Many companies see the end goal of digitalization as the ability to provide workers with connected devices that display real-time data and insights to help them perform faster and more effectively. This hands-on digitalization should cover everything from scrutinizing raw material supplies to tracking customer deliveries and everything in between.
4. Cybersecurity needs to be in focus
The more companies integrate their operations digitally, the larger the attack surface becomes, as well as the risk of an intrusion. Cybersecurity is thus a big concern for all the companies we spoke with. An additional challenge is a way in which they are integrating parts of the operations with partners and suppliers. Governments and regulators are setting new rules around cybersecurity and compliance, which adds another dimension to the problem.
Find a partner that can simplify Digitalization
What we took away from our interviews with chemical industry leaders is that they need partners to remove the complexity that will help them get to the next level. To move beyond the OT approach of generating solutions for specific use cases, they need a holistic, platform approach to integrate digital technologies across their operations. This starts with robust wireless connectivity for integrating sensors and running low-latency, high-bandwidth applications. It includes edge solutions for local processing of data, ready access to application libraries and pre-integrated industrial devices to connect workers – all secured against cybersecurity threats. At Nokia we understand that all the ingredients must work as one with legacy machines as well as personnel. We provide one platform for industrial digitalization to make this transformation as simple as possible.
Are you interested in seeing what digitalization trends are on the minds of your peers in the chemicals and plastics industry? Download the full white paper here.