The Metaverse: Industry’s next evolution
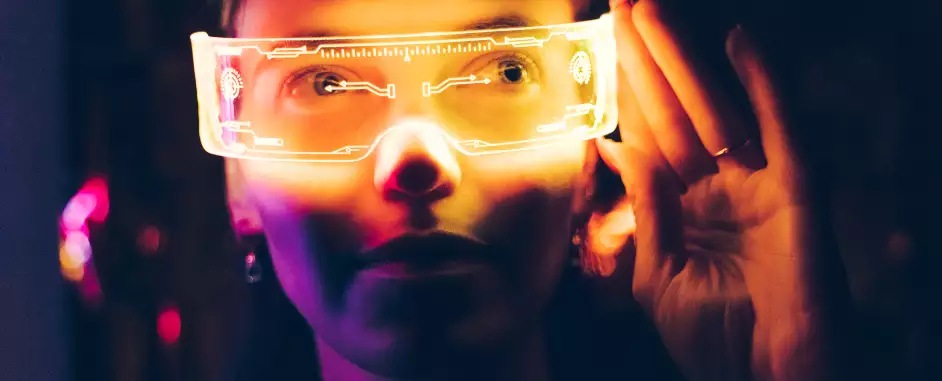
Much of the hype surrounding the metaverse has focused on its potential for interactive and immersive consumer experiences. But what can be said about the promise of this vast, virtual space for asset-intensive industries?
This question is the focus of a recent article in MIT Technology Review featuring perspectives from Raghav Sahgal, President of the Cloud and Network Services business at Nokia, and Thierry Klein, President of Bell Labs Solution Research at Nokia Bell Labs. The piece describes how digital twins, as an early application of the industrial metaverse, are already revolutionizing enterprise operations across industries. Examples are shared from Boeing and BMW and the article examines why immersive data-rich tools are well-positioned for broader adoption.
Many significant business benefits await in the industrial metaverse and Industry 4.0 digitalization sets a path for realizing these advantages.
So much of the hype surrounding the metaverse has focused on its potential for interactive and immersive consumer experiences. What can be said about the promise of this vast, virtual space for manufacturing, transportation, logistics and other industries?
A metaverse of possibilities for industries
Enabled by a confluence of network, communication and cloud technologies, the metaverse empowers industries to shift expensive, time-intensive activities into a fully virtual world. Activities like prototyping and testing are far more flexible and accessible in a digital format, allowing industries to iterate, experiment and validate like never before. As Raghav Sahgal noted, “The use cases are infinite, quite frankly, because you can apply it (the metaverse) to almost any industry.”
Most of the use cases possible today involve creating digital instantiations of physical assets – (manufacturing production lines for example) in the application of digital twins. This brings substantial benefits over traditional prototyping when combined with real-world data - and when the digital twin becomes immersive and three-dimensional. It simulates and predicts how an object or process will function as a physical, fully realized entity. Companies can run test after test, iteration after iteration, until they get the best outcome for their operation. This removes the guesswork and capital involved in reconfiguring physical operations to test new models.
Beyond manufacturing, in the logistics industry, companies can create a digital twin of their operation flows using data from within the warehouse and from across the extended supply chain for better operational decision-making, enhanced processes, productivity and resilience.
Railways can leverage digital twins to optimize maintenance and uptime of rolling stock and rail infrastructure, and improve customer experience and safety in stations. Industrial metaverse-enabled digital twins can optimize passenger flow, and improve the management of complex timetables, identifying conflicts and “trickle-down” congestion scenarios. The list of use cases across industries goes on and on.
While these examples help visualize the opportunity, the industrial metaverse extends beyond digital twinning to other valuable applications like 3D instructional work orders, training and collaboration. Workers stand to benefit from augmented, engaging on-the-job instruction with real-time access to experts for questions and consultation – speeding job processes, new technology onboarding and new hire training. Metaverse-enhanced remote collaboration allows workers to engage virtually alongside each other with artificial intelligence, speeding problem-solving and information sharing using intelligent, dynamic analytics living in the cloud.
The benefits of boundless space, and the role of the Metaverse and Industry 4.0
With the ability to iterate infinitely, industries can innovate freely and at the same time ensure worker safety - making it possible to run scenarios that would be difficult or even dangerous to train for in the real world. Imagine the massive benefits for public safety agencies and the mining industry. In a digital environment, storing massive amounts of data allows for automated analysis, planning, forecasting, and decision-making that is significantly faster and better informed.
With its use of IoT sensors, artificial intelligence (AI), machine learning (ML), pervasive data and other advanced technologies, the industrial metaverse and Industry 4.0 share the same vision of intelligent, connected and resilient operations. As a natural extension of Industry 4.0, the metaverse advances the vision with a “virtual first” approach.
Enabling the metaverse
What do industries need to have in place to take full advantage of the opportunities in the metaverse?
According to Thierry Klein, the networking and compute needs of the metaverse “will be pretty immense in terms of the data and video consumption,” Fast data transfer speeds across wired and wireless networks are a must, with 5G investments being essential to enable the low latency and precise data exchange the metaverse demands.
Given the need for near-zero latency, the metaverse is also dependent on edge computing — with decentralized local edge data centers closer to users — as well as an agile cloud infrastructure to connect private and public clouds. To feed data into the virtual world, advanced sensors, Artificial Intelligence (AI) and machine learning tools interpret collected data and automate the physical world to respond to it. A programmable, network-as-code and software-as-a-service approach, exposes network capabilities to allow for greater experimentation, innovation, flexibility and modularity.
Getting your operation to this point may be closer than you think. The foundational network technologies needed to set the stage for the industrial metaverse are available now. With advanced industrial networks built on fast, flexible 4G/5G private wireless, high-performance IP/MPLS and optical transport, industrial edge computing and more, asset-intensive enterprises can experience the benefits of digitalization today while preparing to capitalize on the innovations and opportunities presented by the industrial metaverse and the 4th industrial revolution.