How digital twins are driving the future of engineering
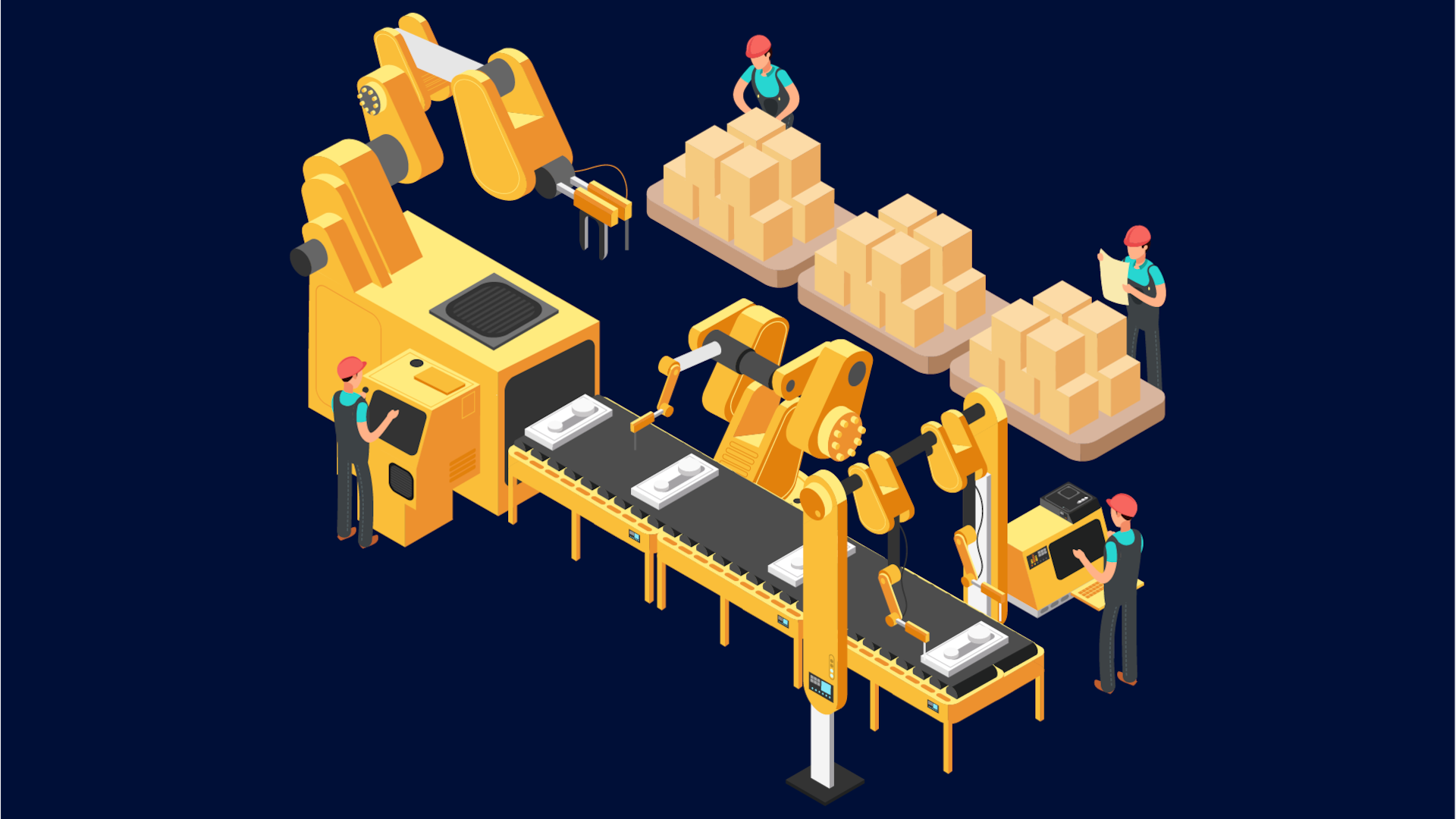
Marshall McLuhan once famously observed, “First we build the tools, then they build us.” Building on artificial intelligence (AI), the Internet of Things (IoT), and 5G communications, advanced software systems are remaking the nature and complexity of human engineering. In particular, digital twin technology can provide companies with improved insights to inform the decision making process.
In this day and age, processes and machines are so complex that the risks of failure or disruption from experimenting with different approaches becomes too high or costly. To use an old analogy, it’s tough to change the wheels on a moving train. And that can be frustrating when new designs might provide significant benefits to existing systems.
Digital twins are an exact replica of something in the physical world. It provides data-driven representations of physical systems using IoT sensors and analytics. Beyond inert computer-aided design (CAD) models, digital twins offer engineers virtual tools for managing assets and resources while improving performance. Companies develop digital twins by attaching sensors to their products and equipment in order to monitor systems and model system dynamics. In one example, a digital twin of an aircraft’s engine enables pilots to monitor the health of an engine in real time.
More than a blueprint or schematic, a digital twin combines a real-time simulation of system dynamics with a set of executive controls. Serving as both an interactive simulation and a set of administrative tools, digital twins manage facilities, systems, and machines, while gathering data to drive performance. Using digital twin technology to manage entire factories, companies like Siemens are simulating and testing systems at the level of individual machines. General Electric has built digital twins of jet engine components that predict their remaining life and the optimum maintenance intervals.
Digital twins are data-driven learning systems
Digital twins are reshaping the foundations of engineering by combining data from human experts with machine intelligence to drive the evolution of work in new and unexplored ways. By detecting anomalies and automating repair processes, digital twins can model and simulate entire procedures and processes. Most importantly, the technology enables firms to anticipate problems and prevent mistakes before they occur.
Digital twins consist of three components:
- A data model
- A set of analytics or algorithms
- A set of executive controls.
A key feature of any IoT implementation, digital twin technology enables companies to simulate processes and improve operations over time. Manufacturers tend to use digital twin technology to improve operations such as plant processes and machine performance in order to optimize supply chains.
Gartner predicts that by 2021 half of all large industrial companies will use digital twins. This is in large part because digital twins are now driving new business models and evolving industrial automation. Despite this, many businesses have been slow to embrace digital twin technology because it is complicated to implement. Once implemented, however, digital twin technology can add value to traditional analytical approaches by improving situational awareness.
From industrial planning and manufacturing to wind farms and industrial agriculture, digital twins provide real-time and predictive analytics that measure and optimize the operation of engineered systems and processes. These virtual doppelgangers assist industry personnel to test systems virtually before applying changes in the physical world. Lessons learned in the virtual world can be invaluable in improving machines and systems in the physical environment.
Using augmented and virtual reality (AR/VR), digital twins offer tools for training and for accelerating the learning capacities of an organization. Merging digital twins with AI and machine learning, digital twins can feed on multiple data in order to improve real-time working functions. Digital twins draw data from a number of sources, including real-time control systems, historical sensor data, and asset management systems.
Digital twin technology is dramatically reshaping the design and engineering process, but it is not radically new. Virtual and simulated software environments have existed in some form for decades. In one example, product and process engineering teams have used CAD models to support systems engineering since the 1970s. However, what is new about today’s Digital Twin technology is its capacity to harness real-time data to drive learning and improve overall performance.
Data + automation
Where operations may have previously run manually, digital twins are helping to drive the shift to automation. Bringing together hardware, software, and data, digital twins enable engineers to optimize the design and operation of a product or service in real time. Digital twins build on AI, IoT, and software analytics to create living digital simulations that interactively update and evolve with their physical counterparts. Using an input created by an AI-based technique called inferred measurement, for example, operators can combine actual measurements with AI-driven data.
Creating a digital twin network means new opportunities for monetizing data.
Rooted in the logic of IoT systems, digital twins enable machine-to-machine learning systems in order to reduce errors. Developing and supporting digital twins requires the continuous updating of data, both in terms of ongoing operations, and in terms of adaptive analytics and algorithms. Data empowers digital twin technology by providing networked software systems with the resources to accelerate decision-making. If manufacturing equipment is lagging, for example, data can signal the need for machinery to be fixed or upgraded before impacting operations.
AI, machine learning, and other advanced technologies use digital twin models to suggest improvements to operations. Leveraging sensor data and user feedback, digital twin technology can assist engineered systems to independently “learn” and improve performance over time. This involves integrating historical data from past machine usage with human data and machine learning algorithms to monitor performance in real-time.
The use of digital twins ensures that data is always flowing. And creating a digital twin network means new opportunities for monetizing data. Consider that in 1976, only 16 percent of the S&P 500 was made up of intangible assets (patents, trademarks and copyrights). Today it is 90 percent. What this means is that intellectual property and the data it protects are now the world’s most important commercial and national security assets. And all of this data is driving new systems of automation.
Beyond machines
Digital twins are not confined to machines or inanimate objects. Where the technology was once limited to aerospace and heavy machinery, digital twins have now become fundamental to a wide range of engineering domains.
In the context of healthcare, a digital twin can monitor and manage a patient’s vital data using a biophysical model. Linking sensor data to cloud-driven analytics, a doctor can provide the most current treatment in managing a patient’s healthcare at a distance. A virtual replica of a patient’s organs allows surgeons and health professionals to practice procedures in a simulated environment rather than on a real patient. In fact, digital twins are expected to combine with genomics and machine learning to revolutionize healthcare operations and improve patient care.
Digital twins in telecommunications
In the telecommunications industry, a digital twin can monitor and manage complex telecom networks, while also gathering data from social media. As operators add layers of technology, including connected devices and additional spectrum bands, a digital twin can monitor and augment these complex systems in real-time. Nokia, for example, has introduced Nokia 5G Digital Design concept to simulate 5G use cases. Using machine learning algorithms, the platform can leverage digital twin technology to quickly monitor and assess the impact of 5G implementation, while providing automated recommendations.
Digital twins have now become fundamental to a wide range of engineering domains.
In another example, Nokia, in collaboration with BOSCH, has been researching the use of 5G for industrial automation and control systems in manufacturing. Some of this work has been incorporated into a proof-of-concept system that was demonstrated at MWC 2019.
This automated line contains sensors for each part of the production process that feeds data to a controller. The information is then transmitted over the 5G link to an industrial control pad that displays a digital twin of the machines, showing key performance data and allowing adjustment of operating parameters in real-time. This type of data allows the machine operators to monitor and control multiple areas of a manufacturing process without having to access individual data per machine, reducing the workload and providing a more accurate picture of the current operational status.
High-fidelity digital twins are becoming easier to create and maintain as IoT implementations expand access to big data and vast digital ecosystems. Going forward digital twin technology is emerging as one of the key software tools in revolutionizing product development. But it is also reinventing the space of work itself.
“First we build the tools, then they build us.”
In its scope and complexity, this software-driven transformation may be unlike anything we have experienced before. Bringing together hardware, software, and data, digital twins drive the optimum design and operation of a product or service. Digital twins represent a fundamental shift in the scope and scale of engineering. But they also enable a transformation in the scale of the human imagination.