Digital twins in manufacturing
Real Conversations podcast | S5 E4 | February 16, 2023
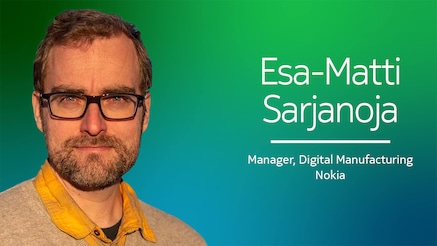
Biography
Esa-Matti Sarjanoja is the Manager, Digital Manufacturing and Connectivity, Manufacturing Solutions, at the Nokia Oulu Factory for Nokia. Before joining Nokia, Esa-Matti spent ten years working on IoT at VTT Technological Research Centre of Finland. After joining Nokia in 2017, Esa-Matti began work on digitalizing the Oulu factory production as a lead developer and is now currently leading a team of highly skilled professionals at the Oulu factory specializing in software developers and private wireless experts.
Digital twins have been around for some time but Esa-Matti Sarjanoja, who is based in Oulu – at what the World Economic Forum called out as Nokia’s ‘factory of the future’ – is taking things to the next level. Previously a researcher on the Internet of Things, he began building a digital twin of all factory devices and is now working to introduce new, cutting-edge products to market.
Below is a transcript of this podcast. Some parts have been edited for clarity.
Michael Hainsworth: Oulu, Finland, population 200,000. On the outskirts of the city, north of Helsinki, sits the factory of the future. It's producing base stations for Nokia and producing insights into the Fourth Industrial Revolution thanks to its digital twin technology. Esa-Matti Sarjanoja is the manager of Digital Manufacturing for Mobile Networks there, and his research is so advanced, he's already working on the next generation of the technology that makes it a facility that's both a factory and a laboratory.
Esa-Matti Sarjanoja: We are a new product introduction (NPI) factory. And that means that we are, in a way, like a laboratory, as you mentioned for our R&D. So basically, we ramp up how to manufacture these base stations. But then again, we also have some volume production. So basically, NPI, a new product introduction factory.
MH: And that gives you the ability to learn as you go while exploring what the opportunities are within the Fourth Industrial Revolution?
EMS: That is correct. But then again, if we are talking about us as a laboratory, we are still a manufacturing unit. All the things that we do, all the software that we create has a price tag, and that reflects on the prices of how much it costs to manufacture these base stations. So basically, all the Industry 4.0 initiatives that we have taken must have a payback time.
MH: A factory like this requires a lot of Internet of Things (IoT) based technology. What's your background?
EMS: That's right. Before I joined Nokia, about five years ago, I was working for VTT Technical Research Centre of Finland Ltd. I was doing IoT related research there for approximately 10 years. Since I joined Nokia, first, as a lead developer, we started to build the digital twin of all factory devices, on top of my former knowledge. But now, I lead a team of highly skilled experts doing the same thing.
MH: The concept of a digital twin is already in its second generation. Tell me what a digital twin really means to you.
EMS: Yeah. A digital twin, in my opinion, is more of a data-related thing. The thing that you see from an iceberg. I mean that sometimes, people refer to digital twins as augmenting real-time metrics on top of a 3D model. But in my opinion, there are things that you don't see; how to model physical assets, or in our case, also non-physical assets such as software components and factory operational processes. How we model those, is that we can model the parameters, the telemetry, the components that the assets or the digital twins consist of, relationships to other assets. And, the command layer, how to talk back to the devices.
MH: Oh, that's fascinating because I can imagine a lot of us would think of digital twins as being focused primarily on monitoring how an assembly line works, making sure that the sprockets are turning properly and when they might wear down, and how to replace them before that breaks down so that you can ensure a smooth-running factory. But you also have System on a Chip (SoC) technology with firmware. You've got computers that run operating systems. You would have to keep track of all of that, too.
EMS: Yes, that is correct. You mentioned the sprockets running in the production of, and I also said that we don't necessarily mean that a digital twin is augmenting things on top of 3D models, but we do have that also. But this is the presentation layer to what we have stored in our digital twin. So, you mentioned how to monitor how production lines are working and so on, how to predict in advance if something is going to be happening in production. These are the things that we are trying to solve, and somewhat have been solving with our digital twin core.
MH: I can imagine you can't really do a lot of that work without standardization. What role does standardization play in ensuring the smooth functioning of a factory in the Fourth Industrial Revolution?
EMS: Yes. That is also a very good question because we have been struggling a bit with the standardization of digital twin models. When we started, there were basically two different competing models, and we selected the one that has a commercial background, but which is still open source. So, we have a definition that is supposed to be compatible with the definition that the other companies are using. In terms of whether we are looking into, for example, metaverse, I think that these things have to be decided together.
MH: So, there's a collaborative advantage to working with partners.
EMS: Exactly. If we were to share information with our partners, they have to be somewhat compatible with the way we are doing things. Of course, the interfaces that we have are standard already in how the interfaces work. But then again, the way we model our digital twins, it also must not be our own thing that we only use for ourselves.
MH: I want to get deep into the particular abilities and the use cases of your digital twins. But before I do, I'm fascinated by your partnership with Microsoft, speaking about a collaborative advantage. You've got the Microsoft Azure platform and Chat-Based Generative Text Prediction (ChatGPT). I guess, it's one thing to have an IoT dashboard for the factory, but to be able to ask the factory a question and get a detailed answer, I guess that takes the Fourth Industrial Revolution really to that next level.
EMS: Yeah, you are correct. And I wouldn't say that we are already there, but this is the way we are heading now. So, in fact, we do have access to that Azure Open AI platform. And this is what we are using to make it possible for our factory personnel, who are not always ‘technical’ or computer-savvy. We want them to be able to ask questions in plain English and get results in plain English. And, having all the data in a single format in our digital twin core makes this hugely easier, so we don't have to capture the data from millions of different data sources. Our algorithm has to be compatible with only one or two.
MH: It's an important issue in the world of AI to ensure that the algorithm you're creating isn't a black box. That you have an understanding as to why it did what it did or why it said what it said. It sort of reminds me of the TV show Westworld, where the scientists are debugging the AI of the robots to determine why they said what they said or what they did just by asking them, "Why did you say that?" And you get the answer.
EMS: Yeah, that's a good point.
Speaker 1:
Analysis, why did you ask me about my son?Speaker 2:
We've been talking for some duration, and I haven't asked you a personal question. Personal questions are an ingratiating scheme.Speaker 1:
I see. Continue Dolores.
EMS: I'm a bit concerned about using this, a deep neural network-based algorithms, because you cannot be exactly sure why it is making decisions the way it is? It is somewhat a black box. But then again, we can validate the results ourselves quite easily.
MH: Let's talk about the three key types of use cases; safety and security, productivity, and producing time to market on a prototype, and the operations use case. From what you've learned over the last two years working on this project, which of those use cases has surprised you the most?
EMS: I would say the use cases that surprised me the most are related to how just bringing the data visible to people has a lot of value. Meaning, that our analytics are based on the lead times in our production. I mean, the manufacturing lead time, starting from when the first soldering board starts to get its serial number, until the point where it's packed to our customers. We have created tools to give an overview of that data, but also the capability to deep dive. We are talking about a digital twin of our product in terms of how it moves inside our products. So, we have stored all the actions that have been taken against it. And this has brought up the visibility. As the lead times built up, we have been able to decrease the lead times by 30%.
MH: So, you've reduced the lead time from when a product goes from basically, a little more than a concept to a box that's getting shipped to the customer by 30%. That must be incredible, not just time savings, but cost savings as well.
EMS: Yes, exactly. And thinking about this a bit, we have created, let's say, technologically more advanced use cases on top of our digital twin. But this use case has been the most beneficial for us money-wise.
MH: Safety and security could be broken down, I suppose, into two separate use cases when it comes to digital twins. How are you using digital twins and IoT for safety?
EMS: Well, basically we have two different kinds of indoor positioning systems in our factory. So, we have Automated Intelligent Vehicles (AIVs) which are basically capable of locating themselves very accurately. And then, we have component equipment trains that are operated by factory personnel. And sometimes, when these devices or machines are in the same corridor, sometimes the AIVs just don't know what to do.
But we created a use case on top of that, and we installed a tag on the equipment train so we could track them. And we were able to give commands to the AIV to take a detour if the equipment train is approaching the corridor that the AIV usually uses. I'd say this is the closest example of how we could utilize the digital twin. As we are able to harmonize certain things such as different coordinate systems from this to completely separate systems into a single harmonized form.
MH: What's your favorite use case for digital twins when it comes to security?
EMS: I would say, it’s where we are able to utilize the same core that we are using for monitoring how our placement machines are doing, how the AIVs are doing. We are using the same core to capture cybersecurity-related information from our factory computers.
MH: And so, you need to understand the vulnerabilities associated with that chip so that you can maintain the cybersecurity of the entire factory floor?
EMS: That is correct.
MH: As far as productivity is concerned, tell me a little bit more about how digital twins come into play on Time-to-market (TTM) and the increased productivity that you need to get out of a factory.
EMS: Yeah. I would say that it comes from the collaboration with our supply chain, which we have increased significantly in the last year already. Basically, we have given access to our tools to the closest partners inside Nokia. This has also proven quite successful for us. But of course, we are still waiting for the big fruits to drop from the TTM side. So basically, we would, as I mentioned, try to improve the manufacturing process all the time in cooperation with the R&D, and with the supply chain colleagues. So, what we would like to do is that we would like to connect how our production process affects, for example, the yield.
If, for example, the component vendors, the components and lots change, if there are certain differences between their soldering boards, if we buy them from different vendors, because sometimes these things stack up. We might have certain combinations of components, soldering boards, or stencils that we are using to press the soldering paste into the soldering boards. Sometimes, the combination of these three cause trouble, even though it is specified that we should be fine.
But our board have to be specialists who are highly skilled. In this sense, they might know that you are not allowed to do a combination of this vendor and this board for some reason, because they tend to fail at some point. But here, we are talking about perhaps, tens of thousands of different variables that are, or are not, linked to each other in terms of yield. And we would like to automate this process.
MH: That's really remarkable. I had no idea that you could run into incompatibilities with a certain type of solder, with a certain type of board. And maybe there's one person in the factory who knows this, but if they’re not working that day that you request this necessary equipment, then you're going to have failures at some point down the road. So, this is a perfect use case for AI, IoT, and a digital twin that can recognize well before the product enters the beginning phase of production to ensure that you don't have these failures sometime down the road.
EMS: When we deep dive into some topic that we haven't done earlier on, we just understand how little we actually stand on the field. But this cannot stop us. So, we are not stopping anywhere. We have initiated discussions with, for example, the companies that make our designer tools, and discussed how we could integrate them directly into the tools. If we were to solve the problem I described, we would first start giving advice to our board assembly specialists. But the next step would be giving advice to the designers on their designer tools. But this is a huge leap.
MH: What are the key takeaways for visitors and customers when they come to Nokia Oulu?
EMS: We do have our own share of visitors. We had somewhere around 200 visitors last year, so we have quite a lot of people coming to the factory. And usually, they are amazed at the technological level that we have in the factory. We have AIVs running around, we have robots doing parts of assembly that, earlier on, are done completely by humans. And then, of course, we have private wireless networking, meaning LTE and 5G networking providing connectivity to our devices. On top of everything, we have the digital twin and its use cases that are already used in full production all the time. I can say that some of our customers have asked, "Can we buy this somehow as a part of the Nokia solution?" Well, I can tell, that at least not yet.
MH: So, if there was one takeaway for the listener to this conversation about the next generation of digital twins, what should it be?
EMS: I'm very keen on seeing what the industrial metaverse is going to bring in here. I cannot say that I have really captured what it really means for us, but when it happens, I want to be there.