Lessons for success in Industry 4.0
Real Conversations Podcast | S4 E2 | April 28, 2022

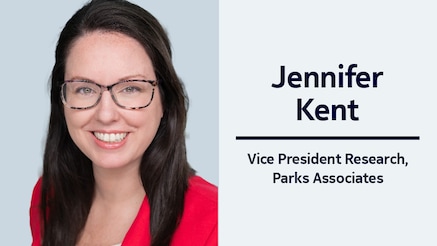
Jennifer manages the research department for Parks Associates, an internationally recognized market research and consulting firm specializing in emerging consumer technology products and services. She leads and advises on syndicated and custom research projects across connected consumer verticals.
Industry 4.0 is top of mind for many organizations. Yet achieving it is never simple. Recent research from Parks Associates highlights the key enterprise roadblocks and how to overcome them. Jennifer Kent, Vice President of Research at Parks, explains more.
Below is a transcript of this podcast. Some parts have been edited for clarity.
Michael Hainsworth: Getting over the “Curmudgeon Effect” is only one hurdle in the way of Industry 4.0. Jennifer Kent of Parks Associates identified the top five roadblocks' enterprises face when launching an initiative. They are networking and the legacy environment, the data, cyber security, vendors, and the way any given enterprise operates. We sat down to discuss those roadblocks — and the secrets to success from those who have already taken the path. In many cases the problems and solutions are consistent across industries. But not all:
Jennifer Kent: Industry 4.0 is at a really interesting stage of deployment. In fact, most companies that are engaging in Industry 4.0, deployments are at various stages, of course, of their deployments and understanding how they can use the technology. We thought it was really important to go out and study what the current roadblocks are, especially as enterprises and municipalities who are deploying these technologies have had a pretty challenging past two years, right? And so, trying to understand if deployments have stalled, if they're moving forward, if they're more important now than ever, and what are the roadblocks there to deployment.
MH: So, we've got energy, we've got manufacturing, we've got a whole host of different industries, but for manufacturing, how friendly to 5G and other IOT based technologies are their plans? It sounds like they've got a problem right out of the gate.
JK: Yes, absolutely. So, when we look at manufacturing and energy and transportation, each of these industries has their own particular challenges in deploying different technologies. Manufacturing's actually somewhat farther ahead than the others because they are a set plant typically, an indoor environment where you can control a lot of the environment.
MH: What about transportation?
JK: Transportation? It's the fact that you're not in one spot, right? And so, there's issues with, so let's say there's transportation, we talked to CIO, a large transportation company that focuses primarily on busing, right? And you're going to different municipalities. You're moving in and out of different ranges of cellular networks, different terminals may have different technologies, networks that you have to log into or log out of, and then of course, that complexity is multiplied when looking at airlines, because now you're out of country and very, very, very different networking environments in different markets and also at different airports. So, one thing that might not be widely known is that airports often are not sharing their network capabilities with airlines. And so, each of these different stakeholders that are coming in and out of an airport are having to deploy and manage their own networking technologies and infrastructure and communication language. And so, a lot of barriers to making, to really, honestly, collecting all the data that they like on their roadmap, to be able to digitalize an entire process through the transportation journey, if you will.
MH: Energy, meantime, we talk about how there's no green without digital, but digitalization of the energy industry has its own unique challenges. What's the one that jumps out at you?
JK: There are challenges from going all the way to the raw materials of mining in the coal mines, and developing a deployment there, all the way to energy distribution. Let's take wind, for example, wind and nuclear. We talked to some technology decision makers that are running wind operations, as well as nuclear plants. So, in wind, you've got a situation where you may have windmills that are two, three kilometers offshore, right? And so you're already out of the range of many deployments of the networks that you might be wanting to rely on. But it's really important, in fact, we found that in the wind industry, 60% of the cost of wind generation is maintenance and operation. Anything that can bring those costs down is enormously beneficial to that industry.
Being able to deploy sensors that understand the temperature, that understand the moisture and the humidity, and actually they're using optics to be able to take pictures, a hundred pictures a minute or so, and then use AI to understand what they're seeing to track corrosion in the windmills and to get it ahead and to be able to plan for corrosion in the windmills. Right? And so it's, again, enormously difficult to do that in an offshore environment. And so there are some technical issues in the windmill, in the wind generation industry that we heard about.
In nuclear, what was really interesting was the mismatch between technology development life cycles and the safety and monitoring needs of spent fuel rods. So spent fuel rods tend to take about 80 years for the radio activity to decay to a safe level. They're actually deploying sensors and monitoring solutions today to be able to track the radio activity levels of spent fuel rods, but they don't have sensors that are going to last 80 years.
Huge opportunity for the industry out there, if you have sensors that can last 80 years in an extremely harsh environment, there's an opportunity for you there. But, but so there's this thoughtfulness and this very, very long-term planning and a need for vendors that can support these types of use cases long term or can kind of match these very specific needs of specific industries.
MH: What's interesting to me is that sure, we talk about the built environment and networking in that there are challenges that are different depending on the industry in which we're looking, but at the same time, when it comes to the other hurdles to adoption that you've researched, it seems fairly universal across the various industries when it comes to data architecture and infrastructure. I'm surprised by the lack of understanding of current critical processes. Is industry simply just too complicated these days for the corner office to understand how everything works?
JK: We absolutely found that data architecture and mapping the data architecture of your Industry 4.0 deployments to actual processes was a disconnect. When we asked for lessons learned, what would you have done differently, there sometimes too much actually of a rush to deploy organization wide, as opposed to taking a step-by-step approach and taking the time to understand what the current critical processes are for your organization that you want to digitalize and starting there. When organizations kind of bit off more that than they could chew, that's when they really ran into problems, ran into wasted investment, those organizations that kind of started with a specific process, tracked the specific process, digitalized that process, and then looked for efficiencies and iterated on that tended to be much more successful.
MH: And I can imagine part of the problem of trying to roll out companywide any Industry 4.0 initiative that involves data is that we've got all these data silos. How do we go from the data silos to data lakes that are necessary to leverage machine learning and artificial intelligence?
JK: That's a great question. So, the reality is that most organizations are working with a mix of legacy technology, legacy infrastructure, and new deployments of new technologies from a wide variety of different vendors. Unless you're dealing with a completely new plant build or commissioning a new nuclear plant. You're going to absolutely be in a situation where you need to integrate legacy and new systems. And what we found is that most of the folks that we talked to who found a way to be successful in integrating their data silos did work with a vendor that could help integrate those technologies or can help them write code that brought together unique systems with a specific application for that organization.
So let me just to give an example specifically from a manufacturer of auto parts who had a pretty nice deployment of technology and tracking of their inventory, and their warehouse and the parts and the components that go into the larger parts that they're assembling and manufacturing. And then you actually have the assembly line, a totally different type of process, totally different type of sensors, totally different of deployment, but for the warehouse and the inventory to know exactly what pieces going on to line and to adjust the inventory in real time has caused enormous savings, to the tune of 20 million dollars a year for this manufacturer. But in order to make their assembly line data talk to their inventory data, the systems that were purpose built for these two different use cases were what they described as 85 to 90% perfect, what they needed, but it's this 10% of how they could communicate them together that really needed some custom codes, some custom support and a specialist who could help them come in and write just what they needed. And then they could replicate that across all of their plants, right? No need to create a custom solution for each of their plants. They could scale it across the organization.
MH: Once we start talking about data, we have to talk about cyber security. With Industry 4.0 and 5G, these are technologies that are broadly cloud native. We have to address the issue of cloud connections and the security therein, but also the operational technologies, not just IT, but OT. And you pointed out there are legacy components, legacy systems that have to be addressed as well. Within cybersecurity and related threats, what do you see as the biggest challenge?
JK: A few things there. So, everybody is very conservative, right? Very nervous about cybersecurity threats, as they need to be. It is itself a roadblock to deployment. There are industries that are extremely sensitive. Every organization feels of course that its data is sensitive, but then you get into critical infrastructure, you get into, again, major safety issues for something, again, like a nuclear power plant. And then regulatory issues. And so that where a new deployment of technology in a particularly hazardous environment may not even be approved by regulators because of cybersecurity concerns and where legacy equipment was all local and not exposed to the internet, new deployments essentially assume some connectivity that's not local. So, what we have found is again and again, our interviewees, through our research, we have found the number one recommendation is network segmentation, right?
Having multiple layers of authorities and permissions to get into critical processes, and then keeping local what needs to be local and having private networks that do that. So, in the nuclear case, of course, anything that actually touches the operation and the production of energy within the plant is in no way connected to the many other processes that are moving to the cloud. So, for instance, any of the HR and the office, the email and the right, systems are absolutely being moved to the cloud, but the onsite plant operations need to be segmented and part of their own network.
Now, one thing that also came up as a barrier is the fact that many of the solutions on market today related to cybersecurity protections are really built with an IT deployment and use cases and personnel in mind and not OT or operational technology, right? And so, we actually found that there is a feeling that there's a lack of vendors with a specialized knowledge in operational technology security.
MH: Right. You can find anybody to secure your email server…
JK: Exactly right. But to find vendors that have that specialized knowledge of securing IOT devices and securing sensors, is a very, very different skill set, and also educating when you bring on a secure operational technology platform into an organization, being able to train the onsite IT staff who are used to dealing with IT developed cybersecurity solutions on the OT solution. So, a little bit of a disconnect there that the industry really needs to work through.
MH: 5G is built with multiple ring fences around its technologies, because we recognized the weak points in legacy networks, but legacy networks aren't going away anytime soon.
JK: That's absolutely right and I think that speaks again and what we heard in our research was to be able to work with vendors that know how to patch these systems who have done it before, who can show proof of concept or speak to integrations that they've done in the past where that knowledge carries forward.
MH: When it comes to the roadblock of people and processes, I suppose we have to talk about managing expectations.
JK: This is a harder one for those in the, you know, who are creating wonderful technology solutions to tackle, but the reality is everybody who's deploying Industry 4.0 against their roadmap is working with an organization of people, they're making decisions, I'm trying to bring people on board, we heard a little bit about trying to tackle the curmudgeon effect, right? There're always those people in the organization who simply don't see the need for change, don't understand, or don't clearly see the return on investment. And of course, have very real concerns about things like cyber security and again, whether or not this is going to be worth it. Oftentimes a really necessary and an important check, and so we found for those, in our research, we found that there were a couple of different really successful ways to bring people in the organization along, and oftentimes that does start with a smaller scale pilot or trial, which allows for a smaller level of investment, but you can prove out the usefulness of the technology. You can test return on investment assumptions, and have a little bit, the proof is in the putting, right, and have the ability to show the data and the learnings, and of course, iterate. You're always going to learn from that pilot what you can do better next time.
We also found that those who involved very different types of stakeholders in the process were successful. So for instance, making sure that there's an actual plant manager, a boots on the ground person who very, very deeply understands the processes that are being digitalized, the challenges that you might run up against in a very practical way is crucial to success, as well as key stakeholders, all the way up into the C-suite who can give the support and the resources necessary for a pilot or full scale deployment in order to, again, kind of get over that curmudgeon effect.
MH: Well, to that point, you touched on return on investment. Every decision is a financial decision. How do we overcome the challenges of estimating ROI and communicating project value?
JK: Yes, actually, a little bit of it goes back to that point about taking specific processes and first understanding the legacy process, right? So, you have to have a baseline to compare against. So, taking the time to understand the process that you're changing or that you're digitalizing, and then moving forward with a pilot allows you to, again, prove out those metrics. Oftentimes also, we heard a lot about making sure that every plant isn't reinventing the wheel, every location, every mining site, right? These are large organizations that operate across countries, and have many, many different plants that let's say may be generating energy in China and in the UK and also in Mexico, and making sure that there's organizational alignment, that when you learn and you prove out in one place, you can do it in multiple different places. And again, everybody's not reinventing the wheel.
It came back to making sure you get a baseline, taking a step-by-step approach and doing pilots that prove it out. And again, maybe not trying to bite off more than you can chew and letting the use case drive your deployment of technology.
MH: We already know that 5G will require CSPs to rebuild themselves to be partnership oriented with both customers and vendors. It's not been a historically strong suit, but what about the Industry 4.0 customers, what's the biggest issue in working with vendors for them?
JK: The biggest issue in working with the vendors that we heard in our research was actually around reliability of the vendor. So there actually is quite a bias towards large traditional established players, and actually this is to the benefit of CSPs, compared to newer organizations who don't have the proven track record, or just even history as an organization, that they will be there for the long term. So, this goes back to the idea of the life cycle of technology being pretty quick, but most of these customers are dealing with product life cycles that are much, much, much longer, and they expect their Industry 4.0 deployments to be serving them for decades, not a few years.
We heard from one mining operation, a big, big leader in global, global, old mining, who, one of the roadblocks that they encountered was working with a vendor who did not have the extensive support capabilities that ultimately they needed. And they felt that they had gone through a good process to understand, oh, yes, of course there are assurances that there would be long-term support. Now, because of that experience, they do an extremely thorough in-depth investigation of an organization's ability to provide support long term, making sure there's not just three people in a back office somewhere that's supporting, there's a full, built out long term plan for support, and obviously that's something that I think positions CSPs really well overall as being a leading type of vendor.
MH: So, these are the top five roadblocks that enterprises are facing in their Industry 4.0 initiatives. What though of the positive Industry 4.0 experiences in your survey sample, which had the biggest impact for an organization?
JK: Yes. It's interesting. We heard so many successes. We're looking for roadblocks, but we heard absolutely awesome successes and really interesting and innovative ways that people are deploying technology. So, we heard a lot about fleets management and people safety. So, using optics to be able to watch drivers and look for sleepiness and make sure that the people are getting the rest that they need, and then setting off automatic alerts and alarms for anybody that has any sort of driver in their fleet of their operation. We heard about technologies being deployed that reduce waste and saving millions and millions of dollars a year, for instance, in a manufacturer who's making tier one supply to the auto industry and talking about how there is a major issue, that most industries are failing these days, around staffing, right?
You hear about the great resignation and everybody's moving jobs, and that impacts everybody. One of the issues is training. So, if you're having more staff turnover a lot of these folks are pretty specialized in their skills and having new operators trying to onboard them and train them in new ways. And so having the capability to have training videos right at each operator's location throughout the plant on every single process and tracking them through the process and surfacing a training video right at the right time really, really an interesting and really impactful and innovative way of applying technology to a people problem.
We have heard a lot about equipment maintenance. One of the I think easiest ways for people to understand a return on investment is making sure that your equipment lasts longer and you're getting the most number of hours out of equipment as, as possible. And so, I think one of the earliest deployments you see across whether it's manufacturing, mining, energy, transportation, is understanding better the equipment life cycle and when something needs to be tuned up and when something doesn't. So, for instance, again, kind of back to the mining industry, the old legacy process for vehicle maintenance was based on hours. So how many hours has this vehicle been operating and when do we pull it to have a tune-up and to do proactive maintenance? Well, now, actually you can look at the filters and say, well, the filters actually aren't dirty enough, and the oil level is just fine, and I can actually get 50 more hours out of this vehicle before I have to pull it for maintenance. So, each one of those changes is interesting.
If you'll allow, I'll give one more really interesting example that I thought was really phenomenal, was applying technology to be able to enable operations that wouldn't be possible based on essentially human decision making and human computation. So for instance, we talked to the CIO of an airline that is specifically focused on their cargo operations, specifically responsible for the cargo operations, and humans tend to be very good at being able to fit cargo into an airplane only to a certain extent, and there's always wasted capacity. And so they've been able to deploy sensors and vision system and AI to be able to actually create what he described as sort of a Tetris optimization, absolutely fitting, selecting the right cargo in the right configuration and packing it in such a way that you're optimizing the space on that aircraft. And of course, every inch of that aircraft in a cargo sense is monetizable, and so you want to absolutely make sure that you're optimizing that space. And it just turns out that humans are not that good at 3D, 4D dimensional computation in real time. So really fantastic application of Industry 4.0 with very clear returns on investment there.
MH: So, of the 30 leaders that you surveyed around the globe in transportation, energy, manufacturing, at the end of the day, what letter grade would you give the leaders you spoke with?
JK: Interesting to grade the leaders. I would say they're all at least at a B plus, if not an A minus, and I would give them that grade, honestly, because they're all very clearly learning and iterating on what they've learned. So not every deployment's been successful, but there's always been a stage two or stage three, or stage four, and this is what we're doing differently, and this is what we've learned. Also very, very eager to share their learnings. So, I don't think that there's a particularly strong sense of proprietary ness or protection around how they're deploying innovation, a strong willingness to essentially talk shop with others and share what they're learning and really move their whole industries forward, which I think is really a great, great leadership.
MH: So ultimately, the best leaders who are doing the best job at rolling out Industry 4.0 initiatives are the ones who have started small, iterated based upon the experiences they've learned, turn the curmudgeons into evangelists, and then figured out what the ROI is and share it with the world.
JK: Great summarization. A lot harder to do than to say, but yes, that's exactly right!